Method for preparing tungsten carbide-cobalt nano composite powder by low-temperature carbonization of solid carbon
A solid carbon and tungsten carbide technology, used in wear-resistant coatings, laser cladding, and cemented carbide fields, can solve the problems of expensive fluidized bed equipment, long reaction time, and high production costs, and achieve controllable free carbon content. Low production cost and small powder particle size
- Summary
- Abstract
- Description
- Claims
- Application Information
AI Technical Summary
Problems solved by technology
Method used
Image
Examples
Embodiment 1
[0050] Embodiment 1: Preparation of WC-10% (m / m) Co nanocomposite powder
[0051] The tungsten-containing compound used is ammonium metatungstate (molecular formula: (NH 4 ) 6 ·(H 2 W 12 o 40 )·4H 2 O), the compound of cobalt is cobalt chloride (CoCl 2 ·6H 2 O), choose water as solvent. According to the requirements of powder composition, the ratio of ammonium metatungstate to cobalt chloride is calculated to be 2.87:1, and the ratio of raw materials to water is (ammonium metatungstate+cobalt chloride):water=3:10. Dissolve ammonium metatungstate in water, add cobalt chloride after it is completely dissolved, and stir the mixed solution evenly; introduce the mixed solution into an atomization dryer to atomize, dry and granulate to make a precursor powder. 350°C, gas outlet temperature 150°C; put the precursor powder into a box furnace and roast at 750°C for 2 hours to obtain a calcined powder; mix the calcined powder with carbon black, and the mixing ratio is calcined p...
Embodiment 2
[0052] Embodiment 2: Preparation of WC-8 (m / m) Co nanocomposite powder
[0053] Ammonium metatungstate and cobalt nitrate (Co(NO 3 ) 2 ·6H 2 O) As a raw material, water is used as a solvent. Raw material mass ratio ammonium metatungstate: cobalt nitrate = 3:1. Dissolve the raw materials in water and stir evenly, then introduce the mixed solution into an atomization dryer to atomize, dry and granulate to make a precursor powder. The inlet temperature is 400°C and the outlet temperature is 130°C; Roasting in a furnace at 600°C for 3 hours to obtain calcined powder; mix the calcined powder with graphite powder in proportion, namely calcined powder: graphite powder = 10:1.18, and ball mill in air for 20 hours to obtain intermediate powder; move the intermediate powder into The thermochemical reaction is carried out in a tube furnace in a mixed atmosphere of hydrogen and nitrogen (1:1). The reaction conditions are: 850 ° C for 3 hours, and the gas flow rate is 10 l / min per kilo...
Embodiment 3
[0054] Embodiment 3: Preparation (WC-10Co)-0.6Cr 3 C 2 Nanocomposite powder
[0055] Raw materials and solvents were ammonium metatungstate, cobalt nitrate, ammonium dichromate ((NH 4 ) 2 Cr 2 o 7 ) and water, according to the mass ratio of ammonium metatungstate: cobalt nitrate: ammonium dichromate: water = 115.3: 49.1: 1.3: 400 to prepare a uniformly mixed precursor solution; the precursor solution is introduced into the atomization dryer and processed Precursor powder was prepared at 390°C and 190°C respectively at gas and outlet temperatures; the precursor powder was calcined at 790°C for 2 hours under the condition of argon gas to make calcined powder; the calcined powder was mixed with amorphous carbon at a ratio of Calcined powder: amorphous carbon = 10: 1.25, and ball milled in gasoline medium for 15h, then reduced and carbonized at 800°C for 4h under the action of hydrogen to obtain (WC-10Co)-0.6Cr 3 C 2 Nanocomposite powder.
PUM
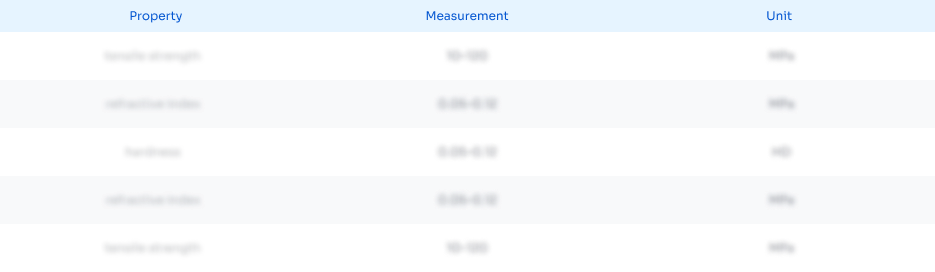
Abstract
Description
Claims
Application Information

- R&D Engineer
- R&D Manager
- IP Professional
- Industry Leading Data Capabilities
- Powerful AI technology
- Patent DNA Extraction
Browse by: Latest US Patents, China's latest patents, Technical Efficacy Thesaurus, Application Domain, Technology Topic, Popular Technical Reports.
© 2024 PatSnap. All rights reserved.Legal|Privacy policy|Modern Slavery Act Transparency Statement|Sitemap|About US| Contact US: help@patsnap.com