Method for preparing metal ceramic gradient coated steel plate by self-stretching continuous mill
A cermet, gradient coating technology, applied in the direction of metal material coating process, coating, metal rolling, etc., can solve the problems of limited mechanical properties of the coating, insufficient pressure, etc., to achieve good fluidity, extended duration, The effect of improving bond strength
- Summary
- Abstract
- Description
- Claims
- Application Information
AI Technical Summary
Problems solved by technology
Method used
Image
Examples
Embodiment Construction
[0029] see figure 1 , The invention relates to a method for preparing a cermet gradient coated steel plate by self-propagating spraying continuous rolling. Its typical embodiment is: fully mix Ti powder, C powder and Ni powder with an atomic ratio of 1:1 to form a powder 3, and send it into the powder feeding pipe of the spray gun, and under the action of the powder conveying gas 2 passing into the pipe, , the mixture of Ti powder, C powder and Ni powder enters the nozzle 4, and then under the action of oxygen-acetylene gas 1 flame heat source, a self-propagating high-temperature synthesis reaction occurs, making it in a molten state or reaching a high plastic state, spraying and depositing To the surface of the steel plate substrate 7 in the hot-rolling humidity range, the molten droplets can continue the self-propagating reaction after being sprayed on the hot-rolled steel plate substrate, prolong the duration of the high-temperature zone, and make the self-propagating cerme...
PUM
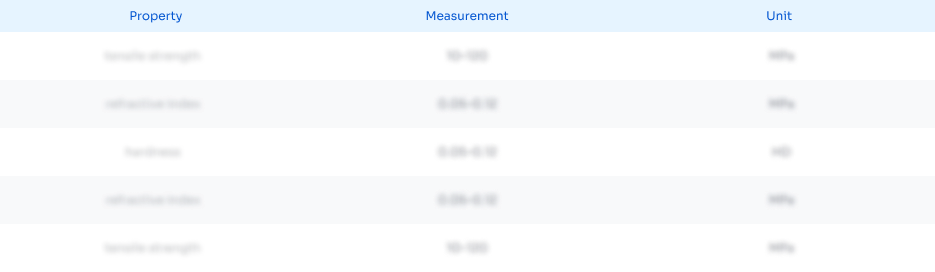
Abstract
Description
Claims
Application Information

- R&D
- Intellectual Property
- Life Sciences
- Materials
- Tech Scout
- Unparalleled Data Quality
- Higher Quality Content
- 60% Fewer Hallucinations
Browse by: Latest US Patents, China's latest patents, Technical Efficacy Thesaurus, Application Domain, Technology Topic, Popular Technical Reports.
© 2025 PatSnap. All rights reserved.Legal|Privacy policy|Modern Slavery Act Transparency Statement|Sitemap|About US| Contact US: help@patsnap.com