Environmental protection high efficiency water finishing paint
A water-based topcoat and high-efficiency technology, applied in the field of paint making, can solve the problems of poor anodic protection performance, high porosity, and lack of electrical conductivity, etc., and achieve excellent electrochemical anti-corrosion performance, excellent organic solvent resistance, and resistivity. Anti-static effect
- Summary
- Abstract
- Description
- Claims
- Application Information
AI Technical Summary
Problems solved by technology
Method used
Image
Examples
Embodiment 1
[0037] The environmental protection high-efficiency water-based finish paint of the present invention, its component weight is Kg:
[0038] Recipe one:
[0039] Silicate solution 60
[0040] Sodium oxide, potassium oxide mixed oxide 20
[0041] Acrylic Emulsion 15
[0042] Isopropanol 5
[0043] Recipe 2:
[0045] Active magnetic powder 30
[0046] Heat resistant iron oxide black 2
[0047] Heat resistant iron oxide yellow 9
[0048] Heat resistant iron oxide green 9
[0049] 1. Add 60Kg of silicate solution in Formula 1, 20Kg of potassium oxide and sodium oxide mixture in metal oxides, 15Kg of acrylic acid emulsion, and 5Kg of isopropanol into the reaction kettle, at a temperature of 50-100°C After mixing and reacting for 3-72 hours, filter after passing the inspection, pack into barrels, and put into storage.
[0050] 2. Put 50Kg of zinc powder, 30Kg of active magnet powder, heat-resistant iron oxide black 2, heat-resistant iron oxide yellow...
Embodiment 2
[0052] The environmental protection high-efficiency water-based finish paint of the present invention, its component weight is Kg:
[0053] Recipe one:
[0054] Silicate solution 50
[0055] Lithium oxide 30
[0056] Acrylic Emulsion 13
[0057] Catalyst, magnesium oxide mixture 7
[0058] Recipe 2:
[0059] Zinc powder 40
[0060] Active magnetic powder 25
[0061] Heat resistant iron oxide black 5
[0062] Heat resistant iron oxide yellow 15
[0063] Heat resistant iron oxide green 15
[0064] 1. Add 50Kg of silicate solution in formula 1, 30Kg of lithium oxide in metal oxide, 13Kg of acrylic emulsion, 7Kg of catalyst and magnesium oxide mixture into the reaction kettle, and mix and react at a temperature of 50-100°C After 3-72 hours, after passing the inspection, filter, pack into barrels, enter the warehouse, and leave the factory.
[0065] 2. Put 40Kg of zinc powder, 25Kg of active magnet powder, 5 heat-resistant iron oxide black, 15 heat-resistant iron oxide ye...
Embodiment 3
[0067] The environmental protection high-efficiency water-based finish paint of the present invention, its component weight percent is:
[0068] Recipe one:
[0069] Silicate solution 45
[0070] Potassium oxide 25
[0071] Acrylic Emulsion 20
[0072] Catalyst, magnesium oxide mixture 10
[0073] Recipe 2:
[0074] Zinc powder 45
[0075] Active magnetic powder 25
[0076] Heat resistant iron oxide black 5
[0077] Heat resistant iron oxide yellow 12
[0078] Heat resistant iron oxide green 13
[0079]1. Add 45Kg of silicate solution in formula 1, 25Kg of potassium oxide in metal oxide, 20Kg of acrylic acid emulsion, 10Kg of catalyst and magnesium oxide mixture into the reaction kettle, and mix and react at a temperature of 50-100°C After 3-72 hours, filter after passing the inspection, pack into barrels, and enter the warehouse.
[0080] 2. Pulverize 45Kg of zinc powder, 25Kg of active magnet powder, 5Kg of temperature-resistant iron oxide black, 12Kg of temperatur...
PUM
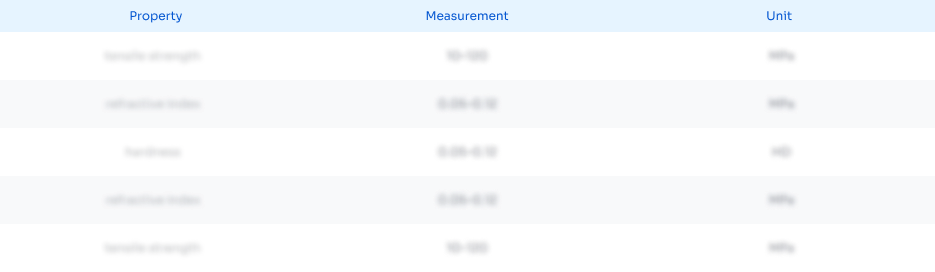
Abstract
Description
Claims
Application Information

- Generate Ideas
- Intellectual Property
- Life Sciences
- Materials
- Tech Scout
- Unparalleled Data Quality
- Higher Quality Content
- 60% Fewer Hallucinations
Browse by: Latest US Patents, China's latest patents, Technical Efficacy Thesaurus, Application Domain, Technology Topic, Popular Technical Reports.
© 2025 PatSnap. All rights reserved.Legal|Privacy policy|Modern Slavery Act Transparency Statement|Sitemap|About US| Contact US: help@patsnap.com