Interface modifier of organic polymer and iron inorganic composite materials and its preparation
A technology of inorganic composite materials and composite materials, applied in the field of interface modifier and preparation, can solve the problems of low piezoelectric performance and magnetoelectric performance, poor interface bonding, etc.
- Summary
- Abstract
- Description
- Claims
- Application Information
AI Technical Summary
Problems solved by technology
Method used
Image
Examples
Embodiment 1
[0026] Example 1: Add barium acetate to the N, N dimethylformamide (DMF) solution of polyvinylidene fluoride (PVDF) and stir to mix. After mixing evenly, heat up to 60°C to 120°C and add glacial acetic acid. After stirring evenly, The titanate is added dropwise according to the stoichiometric amount to form barium titanate, and reacted for 1 to 4 hours to obtain a polymer-containing nano barium titanate sol. Then distill directly at 120℃~170℃, dry for 7~10 days, and grind the mixture into fine powder after complete drying to obtain nano-BaTiO 3 / PVDF in-situ composite masterbatch.
[0027] Weigh PVDF, BaTiO 3 and nano-BaTiO 3 / PVDF, the volume ratio is: PVDF15~50%, nano-BaTiO 3 / PVDF is 1~5%, the rest is BaTiO 3 . After mixing evenly, pour it into a mold, press at 160-200°C for 15-30 minutes, and obtain interface-modified BaTiO after cooling 3 / PVDF composite material, the SEM image of the composite material is shown in figure 1 .
Embodiment 2
[0028] Example 2: Add lead acetate to methanol and stir to mix. After mixing evenly, heat up to 60°C-120°C and add acetylacetone. After stirring evenly, titanate is added dropwise according to the stoichiometric amount of lead titanate, and react for 1-4 hours to obtain Polymer nano lead titanate sol. Then directly distill at 120°C~170°C, dry for 7~10 days, and grind the mixture into fine powder after complete drying to obtain nano-PbTiO 3 . Nano-PbTiO at 500~600℃ 3 Sintering is carried out to obtain nanometer lead titanate ceramic powder. Put the sintered nano-lead titanate into the DMF (N,N dimethylformamide) solution of PVDF, carry out ultrasonic dispersion at room temperature, and spread the film on the glass substrate after the dispersion is uniform. After the film is dried in a drying oven, it is pulverized into powder.
[0029] Weigh PVDF, lead zirconate titanate (PZT), terbium dysprosium iron (Terfenol-D) and nano-PbTiO 3 / PVDF, the volume ratio is: PVDF15~50%, na...
Embodiment 3
[0030] Example 3: Add lead acetate to the N, N dimethylformamide (DMF) solution of polyvinylidene fluoride (PVDF) and stir to mix. After mixing evenly, add zirconium nitrate, heat up to 60°C to 120°C, add acetylacetone, and stir After uniformity, titanate is added dropwise according to the stoichiometric amount of lead zirconate titanate, and reacted for 1 to 4 hours to obtain nanometer lead titanate sol containing polymer. Then directly distill at 120°C-170°C, dry for 7-10 days, and grind the mixture into fine powder after complete drying to obtain PVDF / nano-PZT.
[0031]Weigh PVDF, lead zirconate titanate (PZT), terbium dysprosium iron (Terfenol-D) and PVDF / nano-PZT, the volume ratio is: PVDF15~50%, PVDF / nano-PZT is 3~10%, Terfenol-D 1 to 12%, and the rest is PZT. After mixing evenly, pour it into a mold, press at 160-200°C for 15-30 minutes, and obtain an interface-modified PZT / PVDF / Terfenol-D composite material after cooling, add interface modifiers PVDF / nano-PT, PZT / PVDF...
PUM
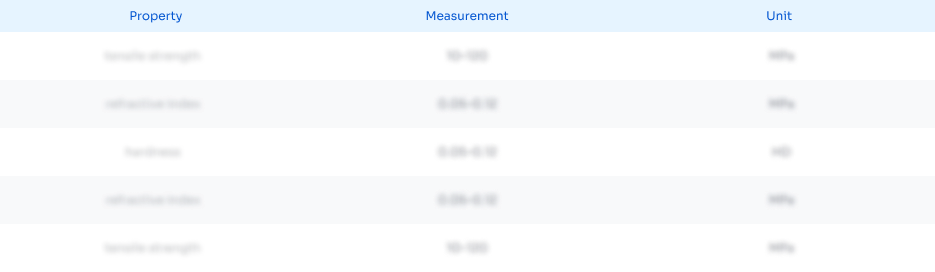
Abstract
Description
Claims
Application Information

- Generate Ideas
- Intellectual Property
- Life Sciences
- Materials
- Tech Scout
- Unparalleled Data Quality
- Higher Quality Content
- 60% Fewer Hallucinations
Browse by: Latest US Patents, China's latest patents, Technical Efficacy Thesaurus, Application Domain, Technology Topic, Popular Technical Reports.
© 2025 PatSnap. All rights reserved.Legal|Privacy policy|Modern Slavery Act Transparency Statement|Sitemap|About US| Contact US: help@patsnap.com