Composite roller for high vanadium high speed steel and its production process
A composite roll and production process technology, applied in the direction of rolls, metal rolling, manufacturing tools, etc., can solve the problems of complex production process, large power consumption, component segregation, etc., to achieve good wear resistance, improve wear resistance, close density effect
- Summary
- Abstract
- Description
- Claims
- Application Information
AI Technical Summary
Problems solved by technology
Method used
Image
Examples
Embodiment 1
[0036] In this embodiment, the roll is divided into a roll core and a roll wear-resistant layer. The roll core is prefabricated with a low-alloy steel material (ZG35CrMo) with good toughness; the roll wear-resistant layer is made of high-vanadium high-speed steel material, and the high-vanadium high-speed steel material The main element content is: C: 1.8%, V: 7%, Cr: 4%, Mo: 3%, Ni: 0.5%, and the balance is iron.
[0037]The production process of the present invention is an induction heating sequential solidification and crystallization method. As shown in the drawings, the casting mold is divided into three sections, which are made of different molding sands. The lower part 7 is water glass sand, the middle part 6 is 80% water glass sand and 20% insulation material, and the upper part 5 is 50% water glass. Sand and 50% insulation material, the base 10 of the mold is provided with a cooling water inlet pipe 8 and a drain pipe 9.
[0038] The specific thermoforming process of...
Embodiment 2
[0041] In this embodiment, the roll is divided into a roll core and a roll wear-resistant layer. The roll core is prefabricated with a low-alloy steel material (ZG40Cr) with good toughness; the roll wear-resistant layer is made of high-vanadium high-speed steel material, and the high-vanadium high-speed steel material The main element content is: C: 2.8%, V: 9%, Cr: 4.5%, Mo: 3%, Ni: 1%, and the balance is iron.
[0042] The production process of the present invention adopts an induction heating sequential solidification and crystallization method. As shown in the drawings, the casting mold is divided into three sections, which are made of different molding sands. The lower part 7 is water glass sand, the middle part 6 is 80% water glass sand and 20% insulation material, and the upper part 5 is 50% water glass. Sand and 50% insulation material, the base 10 of the mold is provided with a cooling water inlet pipe 8 and a drain pipe 9.
[0043] Concrete thermoforming process of ...
Embodiment 3
[0046] In this embodiment, the roll is divided into a roll core and a roll wear-resistant layer. The roll core is prefabricated with a medium carbon steel material (ZG35) with good toughness; the roll wear-resistant layer is made of high-vanadium high-speed steel material, and the high-vanadium high-speed steel material The content of the main elements is: C: 3.4%, V: 11%, Cr: 5%, Mo: 2%, Ni: 1.2%, and the balance is iron.
[0047] The production process of the present invention adopts an induction heating sequential solidification and crystallization method. As shown in the drawings, the casting mold is divided into three sections, which are made of different molding sands. The lower part 7 is water glass sand, the middle part 6 is 80% water glass sand and 20% insulation material, and the upper part 5 is 50% water glass. Sand and 50% insulation material, the base 10 of the mold is provided with a cooling water inlet pipe 8 and a drain pipe 9.
[0048] Concrete thermoforming ...
PUM
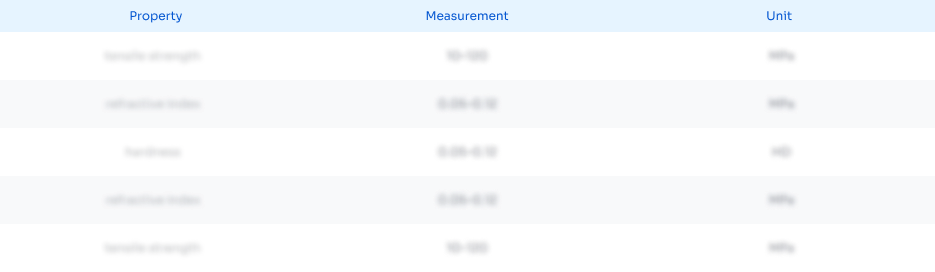
Abstract
Description
Claims
Application Information

- R&D
- Intellectual Property
- Life Sciences
- Materials
- Tech Scout
- Unparalleled Data Quality
- Higher Quality Content
- 60% Fewer Hallucinations
Browse by: Latest US Patents, China's latest patents, Technical Efficacy Thesaurus, Application Domain, Technology Topic, Popular Technical Reports.
© 2025 PatSnap. All rights reserved.Legal|Privacy policy|Modern Slavery Act Transparency Statement|Sitemap|About US| Contact US: help@patsnap.com