Carbonide / iron-base alloy composite coating and its reaction brass coating technology
An iron-based alloy and composite coating technology, which is applied in the coating process and coating of metal materials, can solve the problems of easy contamination of the ceramic/metal bonding interface, insufficient stability of coating performance, and high cost of brazing coating materials. High hardness, good corrosion resistance and low material cost
- Summary
- Abstract
- Description
- Claims
- Application Information
AI Technical Summary
Problems solved by technology
Method used
Image
Examples
Embodiment Construction
[0022] The present invention adopts above-mentioned reactive brazing process, with the industrial iron powder of chemical composition shown in table 1, titanium iron powder, Mo powder, Ni powder, colloidal graphite, boron iron powder, chromium iron powder and Si powder etc. as raw material powder, according to According to the composition ratio in Table 2, the (titanium carbide + chromium carbide) / iron-based alloy composite coating was prepared by reactive brazing on the surface of ordinary low-carbon steel.
[0023] The specific process steps are as follows:
[0024] 1. The material powder is mixed according to the composition ratio, wet milled on a ball mill for 24 hours, the ball-to-material ratio is 4:1, the ball milling speed is 120r.p.m, the ball milling medium is alcohol, and the average particle size of the powder obtained after ball milling is 6-7μm;
[0025] 2. The mixed powder after ball milling is dried in a drying box, the drying temperature is 50°C, and the dryin...
PUM
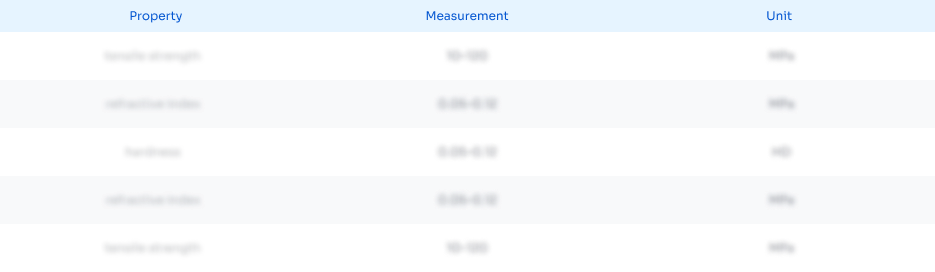
Abstract
Description
Claims
Application Information

- R&D
- Intellectual Property
- Life Sciences
- Materials
- Tech Scout
- Unparalleled Data Quality
- Higher Quality Content
- 60% Fewer Hallucinations
Browse by: Latest US Patents, China's latest patents, Technical Efficacy Thesaurus, Application Domain, Technology Topic, Popular Technical Reports.
© 2025 PatSnap. All rights reserved.Legal|Privacy policy|Modern Slavery Act Transparency Statement|Sitemap|About US| Contact US: help@patsnap.com