Composite hydrosol color fixing finishing agent, synthesizing method and use thereof
A synthesis method and finishing agent technology, applied in dyeing method, fiber treatment, textile and papermaking, etc., can solve problems such as unfavorable industrial production, less obvious color fixing effect, etc., to reduce pollution, reduce washing wastewater, and significantly fix color. effect of effect
- Summary
- Abstract
- Description
- Claims
- Application Information
AI Technical Summary
Problems solved by technology
Method used
Examples
Embodiment 1
[0044] Embodiment 1. Preparation of composite hydrosol
[0045] ①According to γ-glycidyl etheroxypropyl trimethoxysilane: water: hydrochloric acid = 1:20:3×10 -5 Add GPTS and water into a beaker, add dilute hydrochloric acid solution dropwise under magnetic stirring, and stir magnetically at room temperature for 30 minutes to obtain a clear and transparent silicon-containing hydrosol.
[0046] ② According to the ratio of butyl titanate: acetic acid: water: hydrochloric acid = 1: 2.5: 50: 0.014, dissolve TTB in the acetic acid solution, and then add the acetic acid solution of TTB into distilled water containing dilute hydrochloric acid dropwise under magnetic stirring, Stir at room temperature for 30 minutes to obtain a milky white liquid, which is transferred to a separatory funnel, aged for 1 hour, and the lower layer of translucent liquid is taken to form a titanium-containing hydrosol.
[0047] ③ According to the ratio of Si / Ti=5:1 (molar ratio), slowl...
Embodiment 2
[0048] Example 2. Direct dye fixation
[0049]Solophenyl Blue RL (Ciba), Solophenyl Yellow FFL (Ciba), IndosolBubine SF-RGN (Clarient), Turquoise FBL (Taiwan Zhongfu Dyestuff Co., Ltd.), Rose FR (Taiwan Zhongfu Dyestuff Co., Ltd.), Direct Black G ( Zhejiang Tongxiang Dyestuff Factory) prepared 2% (o.w.f) dye solution, the dosage of sodium sulfate was 25g / l, and the bath ratio was 1:20. Dyeing was started at 40°C, and 1 / 2 sodium sulfate and dye were added, and after 10 minutes, the dosage of sodium sulfate was 1:20. Heat up to 98°C at the speed of ℃ / min, add the remaining 1 / 2 yuan Mingfen after 5 minutes, cool to 80°C after dyeing for 40 minutes, take it out and wash it with clean water.
[0050] Finish the dyed fabric with the composite hydrosol obtained in Example 1, and the data of the soaping fastness, rubbing fastness and wet ironing fastness of six direct dyes before and after the sol-gel process are as shown in Table 1:
[0051] dye
So...
Embodiment 3
[0054] Embodiment 3. Reactive dye fixing color
[0055] Respectively prepare 2% (o.w.f) dyeing solution with active green blue B-BEFN, active bright red B-3G, active green blue BES, active bright red BES (Shanghai Wande Chemical Co., Ltd.), and the dosage of sodium sulfate is 40g / l, The dosage of sodium carbonate is 20g / l, and the bath ratio is 1:20. Dyeing at a constant temperature of 60°C, add 1 / 2 yuan of sodium carbonate and dye after 10 minutes of dyeing, add the remaining 1 / 2 yuan of sodium starch after 10 minutes, and then Add sodium carbonate, cool to 40°C after 30 minutes, take it out, wash with water, boil with 1g / l neutral washing powder solution for 1 minute, then fully wash with water, and dry the cloth in the air.
[0056] Finish the dyed fabric with the composite hydrosol obtained in Example 1, and the data of the soaping fastness, rubbing fastness and wet ironing fastness of the four reactive dyes before and after the sol-gel process are shown...
PUM
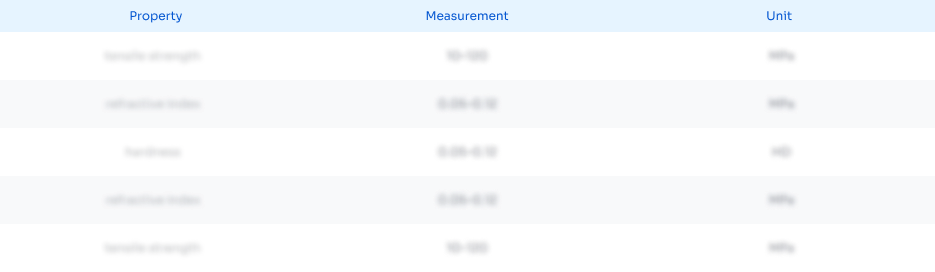
Abstract
Description
Claims
Application Information

- Generate Ideas
- Intellectual Property
- Life Sciences
- Materials
- Tech Scout
- Unparalleled Data Quality
- Higher Quality Content
- 60% Fewer Hallucinations
Browse by: Latest US Patents, China's latest patents, Technical Efficacy Thesaurus, Application Domain, Technology Topic, Popular Technical Reports.
© 2025 PatSnap. All rights reserved.Legal|Privacy policy|Modern Slavery Act Transparency Statement|Sitemap|About US| Contact US: help@patsnap.com