Re-molten spherical alumina casting sand and its prepn
A spherical casting sand and aluminum technology, applied in the direction of casting molding equipment, casting molds, manufacturing tools, etc., can solve the problems of large heat release, low material reuse rate, poor mechanical strength, etc., to achieve rich sources of raw materials, production Low cost and good temperature resistance
- Summary
- Abstract
- Description
- Claims
- Application Information
AI Technical Summary
Problems solved by technology
Method used
Examples
Embodiment 1
[0008] The composition of the remelted aluminum spherical casting sand of the invention is: 70-80% of aluminum oxide, 10-20% of silicon oxide, <5% of iron oxide and <5% of titanium oxide.
Embodiment 2
[0010] The preparation method of the remelted aluminum spherical foundry sand of the present invention is:
[0011] a. Calcining the bauxite ore at 1200-1300 degrees Celsius for 1-2 hours;
[0012] b. The calcined bauxite ore or calcined bauxite tailings are sprayed into balls in a molten state by an electric arc furnace;
[0013] c. Sieve the balls sprayed in b, and take the particles with a diameter of 0.2-1.0 mm to obtain the remelted aluminum spherical casting sand.
PUM
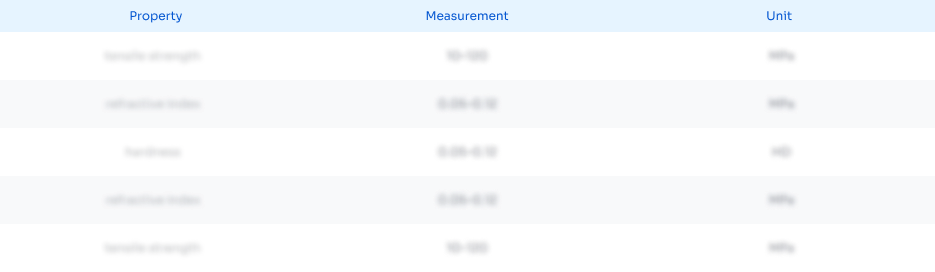
Abstract
Description
Claims
Application Information

- Generate Ideas
- Intellectual Property
- Life Sciences
- Materials
- Tech Scout
- Unparalleled Data Quality
- Higher Quality Content
- 60% Fewer Hallucinations
Browse by: Latest US Patents, China's latest patents, Technical Efficacy Thesaurus, Application Domain, Technology Topic, Popular Technical Reports.
© 2025 PatSnap. All rights reserved.Legal|Privacy policy|Modern Slavery Act Transparency Statement|Sitemap|About US| Contact US: help@patsnap.com