Method of preparing high temperature wear resistant coating
A technology of high temperature resistance and coating, which is applied in the direction of coating, metal material coating process, ion implantation plating, etc., can solve the problems of limited coating thickness, insufficient wear, poor bonding between coating and substrate, etc., and achieve high bonding strength Will not tear, improve work efficiency, and ensure the quality of the workpiece
- Summary
- Abstract
- Description
- Claims
- Application Information
AI Technical Summary
Problems solved by technology
Method used
Image
Examples
Embodiment Construction
[0022] According to the requirements of different workpieces, the preparation process of several technologies adopted in the method for preparing the high-temperature wear-resistant coating of the present invention can be carried out sequentially or alternately, and can also be repeated one or more times.
[0023] The present invention is described in detail below in conjunction with accompanying drawing:
[0024] The present invention is that high-temperature alloy steel workpiece [4] is installed in the vacuum chamber that has magnetron sputtering target [1], electron gun or laser device [2] and ion gun [3] to carry out the preparation of high-temperature wear-resistant coating (see figure 1 and figure 2 ). The production process is:
[0025] Put the substrate [A] on the surface of the workpiece into the vacuum chamber after routine cleaning, and wait until the vacuum degree in the vacuum chamber reaches 10 -3 After pa, ion beam surface sputtering cleaning is performed ...
PUM
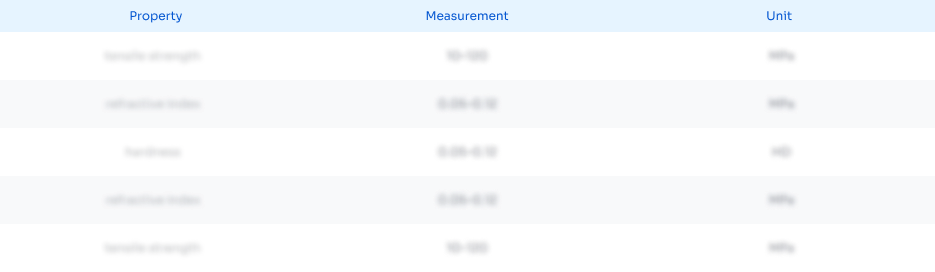
Abstract
Description
Claims
Application Information

- R&D
- Intellectual Property
- Life Sciences
- Materials
- Tech Scout
- Unparalleled Data Quality
- Higher Quality Content
- 60% Fewer Hallucinations
Browse by: Latest US Patents, China's latest patents, Technical Efficacy Thesaurus, Application Domain, Technology Topic, Popular Technical Reports.
© 2025 PatSnap. All rights reserved.Legal|Privacy policy|Modern Slavery Act Transparency Statement|Sitemap|About US| Contact US: help@patsnap.com