Mineral-floating foaming agent and its prepn
A mineral flotation and foaming agent technology, applied in flotation, solid separation, etc., can solve the problems of poor biodegradability, high foam viscosity, difficult defoaming, etc., and achieve good biodegradability, foam toughness and brittleness, The effect of high bubble speed
- Summary
- Abstract
- Description
- Claims
- Application Information
AI Technical Summary
Problems solved by technology
Method used
Examples
Embodiment 1
[0026] The ingredients are mixed according to the weight ratio of isopropanol: propylene oxide = 1:1.1, and at the same time, 0.3% of the total weight of the raw materials is added. Potassium oxide is put into the autoclave, and the reaction is performed at a pressure of 0.5-1MPa and a temperature of 170-190℃. After hours, the pressure was reduced to normal pressure, cooled to 50°C with water, and the catalyst was filtered to obtain a flotation foaming agent product. This product is suitable for flotation of mixed ore containing muddy copper oxide and copper sulfide. Conducive to the recovery of fine-grained gold and silver.
Embodiment 2
[0028] Mix the ingredients according to the weight ratio of isobutanol: propylene oxide: ethylene oxide = 1:1.5:1.5, add 0.6% of the total weight of the raw material amount of sodium oxide, and put it into the autoclave at a pressure of 0.1-1.1MPa, After reacting at 170-190°C for 2.5 hours, cooling with water, depressurizing to normal pressure, and cooling to a temperature of 48°C, filter to remove the catalyst to obtain a flotation foaming agent product. The product has good foaming performance and moderate brittleness, and can be used for the flotation of general copper sulfide ore.
Embodiment 3
[0030] According to the weight ratio of isoamyl alcohol: ethylene oxide = 1:5.5 and add 0.4% of the total weight of raw materials sodium oxide, in an autoclave, react at a pressure of 0.8-1MPa and a temperature of 170-190℃ for 2 hours , Then cool to below 50℃, reduce the pressure to normal pressure, filter to remove the catalyst to obtain the flotation foaming agent product. The foaming property of this product is relatively low, and it has good viscosity, which is suitable for the flotation of general sulfide ore.
PUM
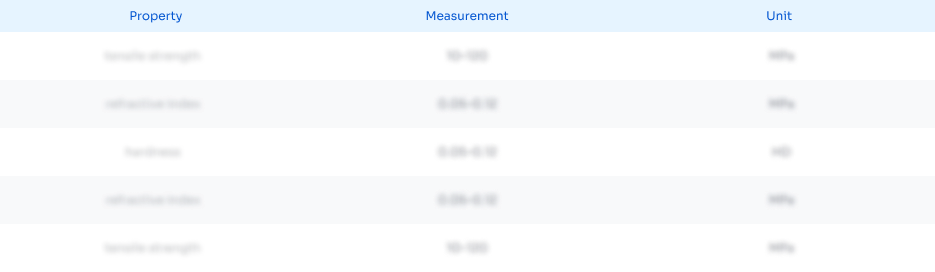
Abstract
Description
Claims
Application Information

- Generate Ideas
- Intellectual Property
- Life Sciences
- Materials
- Tech Scout
- Unparalleled Data Quality
- Higher Quality Content
- 60% Fewer Hallucinations
Browse by: Latest US Patents, China's latest patents, Technical Efficacy Thesaurus, Application Domain, Technology Topic, Popular Technical Reports.
© 2025 PatSnap. All rights reserved.Legal|Privacy policy|Modern Slavery Act Transparency Statement|Sitemap|About US| Contact US: help@patsnap.com