Technical method for producing dihydric alcohol by catalytic hydration of epoxy compound
An epoxy compound, catalytic hydration technology, applied in hydrolysis preparation and other directions, can solve the problems of difficult reaction control, dangerous production, large amount of catalyst, etc., and achieve the effects of mild reaction conditions, economical production and small amount of catalyst.
- Summary
- Abstract
- Description
- Claims
- Application Information
AI Technical Summary
Problems solved by technology
Method used
Examples
Embodiment 1
[0020] Weigh 32.7g of ethylene oxide, 267.3g of water, and 15mg of catalyst ammonium molybdate, add them into a 500ml stainless steel autoclave, control the reaction temperature at 135°C, and the pressure at 1.5MPa, stop the reaction after 30min, and the pressure drops below 1.0MPa, After cooling with cooling water, the reaction product was released. Sample analysis showed that the conversion rate of ethylene oxide was 99.73%, and the selectivity of ethylene glycol was 91.55%.
Embodiment 2
[0024] Weigh 108.2g of ethylene oxide, 445.5g of water, and 100mg of catalyst sodium tungstate, and put them into a 1L stainless steel high-pressure reactor, control the reaction temperature at 140°C, the pressure at 1.5MPa, react for 30min and cool down, take samples for analysis, and convert ethylene oxide The yield is 99.88%, and the selectivity of ethylene glycol is 91.80%.
Embodiment 3
[0026] The 0.012% aqueous solution of potassium molybdate and ethylene oxide are pumped into a stainless steel tubular reactor with an inner diameter of 8 mm and a length of 9 m with a metering pump, the flow rate of the aqueous catalyst solution is 129.5 g / min, and the flow rate of ethylene oxide is 20.1 g / min, the residence time is 3min, the reactor inlet temperature is 150°C, the outlet temperature is 190°C, and the pressure is 3.0MPa. The product is analyzed, and the conversion rate of ethylene oxide is 99.99%, and the selectivity of ethylene glycol is 92.25%.
PUM
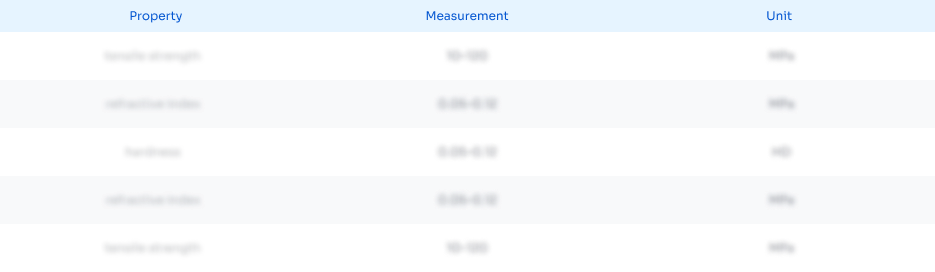
Abstract
Description
Claims
Application Information

- R&D Engineer
- R&D Manager
- IP Professional
- Industry Leading Data Capabilities
- Powerful AI technology
- Patent DNA Extraction
Browse by: Latest US Patents, China's latest patents, Technical Efficacy Thesaurus, Application Domain, Technology Topic, Popular Technical Reports.
© 2024 PatSnap. All rights reserved.Legal|Privacy policy|Modern Slavery Act Transparency Statement|Sitemap|About US| Contact US: help@patsnap.com