Method for preparing selenide or sulfide semiconductor film material of copper-indium-gallium
A copper indium gallium and semiconductor technology, which is applied in the field of preparation of copper indium gallium selenium or sulfide semiconductor thin film materials, can solve the problems of high waste rate in industrialized production, reduced battery manufacturing cost, fragile glass substrate, etc. The ratio and the quality of the formed film are good, the requirements for lowering the ambient temperature, and the effect of overcoming the softening of the glass
- Summary
- Abstract
- Description
- Claims
- Application Information
AI Technical Summary
Problems solved by technology
Method used
Examples
Embodiment 1
[0020] Deposit metal Mo with a thickness of 0.6-1.4 μm on ordinary soda-lime glass, and then deposit copper (0.6-0.8 μm), indium (0.8-1.4 μm), gallium (0.4-0.7 μm) or copper-gallium alloy ( CuGa 0.3 , 1.0-1.5 μm) and indium (0.8-1.4 μm) to form a copper indium gallium metal prefabricated layer. Put the substrate on which the copper indium gallium metal prefabricated layer is deposited layer by layer into a solid-state source light selenization heat treatment vacuum chamber, the back side of the battery substrate is heated by a resistance heat source, and the substrate on which the copper indium gallium metal prefabricated layer is deposited is heated by a halogen lamp or a high pressure mercury lamp Radiation light heating, the wavelength of light radiation is in the infrared to ultraviolet range, when the mechanical pump is linked with the molecular pump or the vacuum diffusion pump to vacuum up to 10 -2 ~10 -5 At Pa, both sides of the battery substrate are heated rapidly a...
Embodiment 2
[0022] Except replacing the solid-state selenium source in embodiment 1 with sulfur, other is the same as embodiment 1, makes Cu(In, Ga)S 2 Compound film material.
Embodiment 3
[0024] If the proportion of chemical elements in the copper indium gallium selenide thin film layer deposited on the glass Mo substrate is out of balance, the selenium content of the thin film layer is insufficient, and when the semiconductor photoelectric thin film material cannot be formed, it can be put into a solid-state source light selenization heat treatment furnace to carry out Secondary selenization, its process is the same as embodiment 1, can adjust the proportioning of element chemical formula composition in the thin film, improves the quality of CIGS semiconductor photoelectric thin film material.
PUM
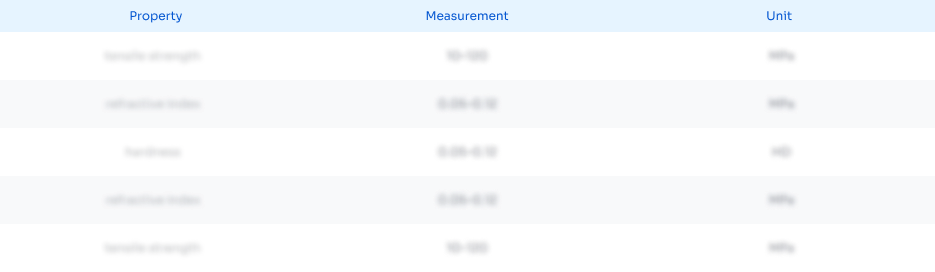
Abstract
Description
Claims
Application Information

- R&D
- Intellectual Property
- Life Sciences
- Materials
- Tech Scout
- Unparalleled Data Quality
- Higher Quality Content
- 60% Fewer Hallucinations
Browse by: Latest US Patents, China's latest patents, Technical Efficacy Thesaurus, Application Domain, Technology Topic, Popular Technical Reports.
© 2025 PatSnap. All rights reserved.Legal|Privacy policy|Modern Slavery Act Transparency Statement|Sitemap|About US| Contact US: help@patsnap.com