Super-fine whirl mill and its non-metallic ore wet method super-fine technology
A technology of flow mill and drum mill, which is applied in the direction of grain processing, etc., and can solve problems such as complex process, easy wear of the pump, and uneven particle size of the product.
- Summary
- Abstract
- Description
- Claims
- Application Information
AI Technical Summary
Problems solved by technology
Method used
Image
Examples
Embodiment 1
[0015] Embodiment 1: its main processing steps are completely consistent with those described in the above description. In step (1), add pulping cylinder 300 orders China Guangdong Shenzhen Longgang heavy calcium carbonate raw material coarse powder is 690 kilograms, and water is 310 liters, and the DA dispersion agent that adds is 3.5 kilograms; Add 150 grams / hour of DA dispersant dropwise in the cylinder; In process step (3), it is 69% (70% lower than the product requirement standard) to measure solid content, so add 33 kilograms of finished product dry powders that particle size is qualified, add DA again 115 grams of dispersants; 72 grams of preservatives are added in the process step (4), after twice homogenizing, the solid content of the product made is 70%, and the viscosity is 250CPS.
Embodiment 2
[0016] Embodiment 2: its implementation process step is exactly the same as described in the above description, and the raw material coarse powder of 350 orders of Lianzhou, Guangdong, China, which adds pulping cylinder in step (1) is 700 kilograms, and water is 254 liters, The DC dispersant that adds is 9.8 kilograms; In the material receiving vat of each mill, drip DC dispersant 700 grams / hour; In process step (3), measure solid content and be 73% (higher than product requirement Standard 70%), so add 46 liters of water, then add 490 grams of DC dispersants; 210 grams of preservatives are added in process step (4), after twice homogenizing, the solid content of the product made is 70%, The viscosity is 220CPS.
PUM
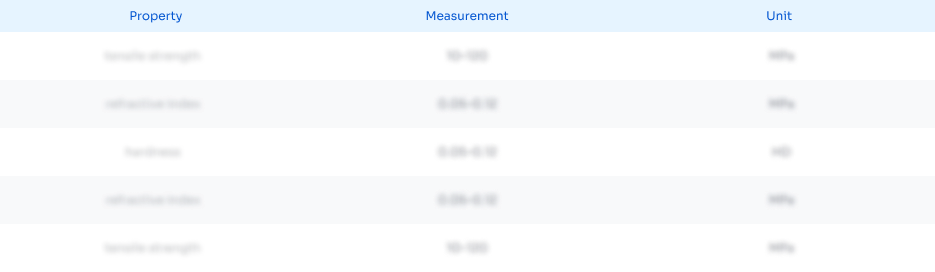
Abstract
Description
Claims
Application Information

- R&D
- Intellectual Property
- Life Sciences
- Materials
- Tech Scout
- Unparalleled Data Quality
- Higher Quality Content
- 60% Fewer Hallucinations
Browse by: Latest US Patents, China's latest patents, Technical Efficacy Thesaurus, Application Domain, Technology Topic, Popular Technical Reports.
© 2025 PatSnap. All rights reserved.Legal|Privacy policy|Modern Slavery Act Transparency Statement|Sitemap|About US| Contact US: help@patsnap.com