Preparation method of multi-component catalyst, multi-component catalyst and application of multi-component catalyst
A catalyst and multi-component technology, applied in chemical instruments and methods, physical/chemical process catalysts, metal/metal oxide/metal hydroxide catalysts, etc., can solve the problem of no multi-component
- Summary
- Abstract
- Description
- Claims
- Application Information
AI Technical Summary
Problems solved by technology
Method used
Image
Examples
preparation example Construction
[0033] In a first aspect, the present invention provides a method for preparing a multicomponent catalyst, the specific method comprising:
[0034] Step S1: prepare a polyacrylonitrile DMF solution, add a nitrogen-containing organic pore-forming agent to the polyacrylonitrile DMF solution, and obtain nanofibers by electrospinning; wherein, the polyacrylonitrile DMF solution is polyacrylonitrile The solution obtained after dissolving in DMF;
[0035] Step S2: calcining the nanofibers at a low temperature and then calcining at a high temperature to obtain an irregularly agglomerated carrier; wherein the temperature of the low-temperature calcination is 190°C-240°C, and the temperature of the high-temperature calcination is 600°C -900℃;
[0036] Step S3: ball-milling the carrier and the mixed metal salt and then calcining to obtain the multi-component catalyst; wherein the re-calcining temperature is 300°C-500°C;
[0037] Wherein, the types of metal elements in the mixed metal ...
Embodiment 1
[0064] Example 1 (experimental group)
[0065] 10 mL of a polyacrylonitrile DMF solution with a mass fraction of 8% was prepared, and 0.5 g of melamine was added to the solution after it was completely dissolved. After stirring evenly, the mixed solution was spun to obtain nanofibers by electrospinning at a voltage of 12.5 kV and a current of 2 mA. The obtained nanofibers were heated to 190°C at a rate of 2°C per minute, calcined in air for 3 hours, then replaced with nitrogen, and heated to 900°C at a rate of 5°C per minute, maintained for 2 hours, and then cooled to room temperature naturally. . The obtained carrier and palladium acetylacetonate, platinum acetylacetonate, ruthenium acetylacetonate, rhodium acetylacetonate are put into the ball mill tank pre-equipped with agate grinding balls, and its total metal mass fraction is 10wt% of the carrier, Pd:Ru: The ratio of Pt:Rh is 1.5:1:1:1, and the ball mill jar is sealed after filling with nitrogen and emptying the air. T...
Embodiment 2
[0067] Example 2 (control group of Example 1)
[0068] This example is a comparative example of Example 1, and the difference between its preparation steps and Example 1 is that in this example, a conventional method is used to mix the multi-component metals (that is, adding the mixed metal salt to the carrier dispersion and stirring and ultrasonically dispersed evenly), the specific steps are as follows:
[0069] 10 mL of a polyacrylonitrile DMF solution with a mass fraction of 8% was prepared, and 0.5 g of melamine was added to the solution after it was completely dissolved. After stirring evenly, the mixed solution was spun to obtain nanofibers by electrospinning at a voltage of 12.5 kV and a current of 2 mA. The obtained nanofibers were heated to 190°C at a rate of 2°C per minute, calcined in air for 3 hours, then replaced with nitrogen, and heated to 900°C at a rate of 5°C per minute, maintained for 2 hours, and then cooled to room temperature naturally. . Disperse the...
PUM
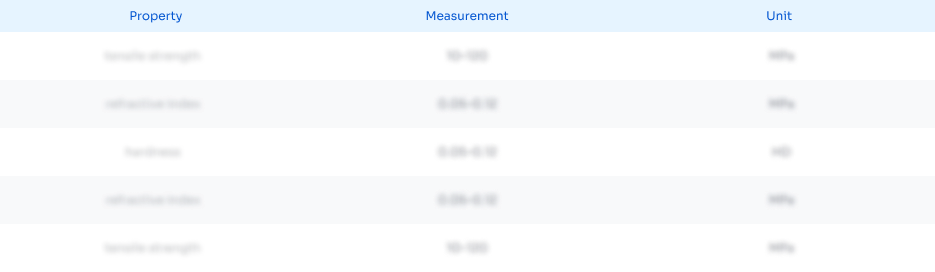
Abstract
Description
Claims
Application Information

- R&D Engineer
- R&D Manager
- IP Professional
- Industry Leading Data Capabilities
- Powerful AI technology
- Patent DNA Extraction
Browse by: Latest US Patents, China's latest patents, Technical Efficacy Thesaurus, Application Domain, Technology Topic, Popular Technical Reports.
© 2024 PatSnap. All rights reserved.Legal|Privacy policy|Modern Slavery Act Transparency Statement|Sitemap|About US| Contact US: help@patsnap.com