High-strength steel plate processing technology
A high-strength steel plate and processing technology, applied in metal processing equipment, manufacturing tools, furnaces, etc., can solve the problem of no waste gas treatment, and achieve the effect of promoting full contact, improving treatment efficiency, and accelerating treatment efficiency.
- Summary
- Abstract
- Description
- Claims
- Application Information
AI Technical Summary
Problems solved by technology
Method used
Image
Examples
Embodiment 1
[0039] refer to Figure 1-8 , a high-strength steel plate processing technology, the processing steps are as follows:
[0040] S1: place each metal raw material in the smelting equipment for smelting, adjust the internal vacuum to 0.04Pa, and pump the waste gas in the smelting box 18 through the first pipeline 20 and the second pipeline 21 into the gas accumulator 22 by the air pump 19 , and then ejected through the first air pipe 26 to form bubbles, which are fully integrated with the disinfection filtrate in the treatment box 2 to process the exhaust gas, and the output shaft of the motor 4 drives the main shaft 5, the sleeve 6 and the plurality of stirring blades 7 to rotate. , agitate the liquid and air bubbles in the treatment box 2 to speed up the exhaust gas treatment efficiency, and at the same time, through the transmission cooperation of the pulley 16 and the belt 17, the reciprocating screw 8 is rotated, and under the reciprocating thread, the reciprocating collar 9 i...
Embodiment 2
[0055] refer to Figure 1-11 , a high-strength steel plate processing technology, the processing steps are as follows:
[0056] S1: place each metal raw material in the smelting equipment for smelting, adjust the internal vacuum to 0.04Pa, and pump the waste gas in the smelting box 18 through the first pipeline 20 and the second pipeline 21 into the gas accumulator 22 by the air pump 19 , and then ejected through the first air pipe 26 to form bubbles, which are fully integrated with the disinfection filtrate in the treatment box 2 to process the exhaust gas, and the output shaft of the motor 4 drives the main shaft 5, the sleeve 6 and the plurality of stirring blades 7 to rotate. , agitate the liquid and air bubbles in the treatment box 2 to speed up the exhaust gas treatment efficiency, and at the same time, through the transmission cooperation of the pulley 16 and the belt 17, the reciprocating screw 8 is rotated, and under the reciprocating thread, the reciprocating collar ...
PUM
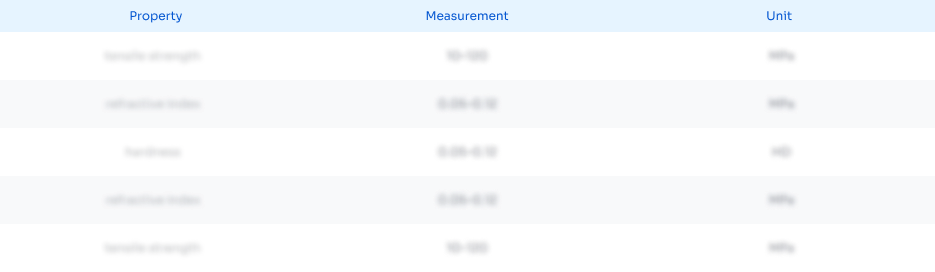
Abstract
Description
Claims
Application Information

- Generate Ideas
- Intellectual Property
- Life Sciences
- Materials
- Tech Scout
- Unparalleled Data Quality
- Higher Quality Content
- 60% Fewer Hallucinations
Browse by: Latest US Patents, China's latest patents, Technical Efficacy Thesaurus, Application Domain, Technology Topic, Popular Technical Reports.
© 2025 PatSnap. All rights reserved.Legal|Privacy policy|Modern Slavery Act Transparency Statement|Sitemap|About US| Contact US: help@patsnap.com