Solar power generation component manufacturing device
A technology for manufacturing devices and components, applied in the field of solar power generation components manufacturing devices, can solve the problems of casting groove processing, difficult assembly, large depth, etc., and achieve the effects of stable and reliable processing, good sandblasting effect, and simple process
- Summary
- Abstract
- Description
- Claims
- Application Information
AI Technical Summary
Problems solved by technology
Method used
Image
Examples
Embodiment 1
[0045] In this embodiment, a manufacturing process for solar power generation components is proposed, which includes the following steps:
[0046] S1: First use mechanical processing, arrange the mold 2 to be processed on the milling machine, use the milling machine to process, and mill the cavity 21. The structure of the mold 2 refers to figure 2 ;
[0047] S2: Prepare the tool electrode 200. The tool electrode 200 is made of one or both of copper, graphite and copper-tungsten alloy. The structure of the tool electrode 200 is the same as that of the radiator shell 1. Etching processing, the casting grooves 22 for forming the heat sink 11 are machined on both sides of the cavity 21, and the structure of the heat sink shell 1 refers to figure 1 ;
[0048] S3: Use high-speed sand flow to blast the inner wall of the cavity 21 and the inner wall of the casting groove 22 to improve the cleanliness and roughness of the inner wall of the cavity 21 and the inner wall of the casting...
Embodiment 2
[0051] refer to image 3 , in this embodiment, a solar power generation component manufacturing device is proposed, which includes a frame 100 and a lifting mechanism 110. The lower end of the lifting mechanism 110 is equipped with an electrode chuck 140, and the electrode chuck 140 is used to clamp the tool anode 200, the tool The electrode 200 is arranged horizontally, the frame 100 is equipped with a water tank 120, the water tank 120 is arranged below the lifting mechanism 110, the water tank 120 is arranged horizontally, and a fixture 130 is installed at the bottom of the water tank 120, and the fixture 130 is used for clamping the mold 2 to be processed, the mold 2 The position corresponds to the position of the tool anode 200. The mold 2 has a cavity 21 in the middle. The mold 2 is in a state in which the cavity 21 is opened in the water tank 120 and is horizontally arranged. The length direction of the tool electrode 200 is consistent with the length direction of the mo...
Embodiment 3
[0062] refer to Figure 4 to Figure 7 , in this embodiment, a process for preparing tool electrodes is proposed, including the following steps:
[0063] S21: Preparation of connecting plate 220:
[0064] 1): First, the selected conductive material is processed into a board with a preset size, then the two sides of the board are smoothed, and the two sides of the board are recorded as the A board surface and the B board surface respectively. Mounting grooves 224 for mounting the fins 210 are milled on the surface of the A board in sequence. There are two rows of the mounting grooves 224. The two rows of mounting grooves 224 are spaced along the width direction of the A-board surface, and the two rows of the mounting grooves 224 are along the width of the A-board surface. The central axis in the length direction of the board surface is symmetrically distributed, each row of installation grooves 224 is arranged along the length direction of the A board surface, and the spacing b...
PUM
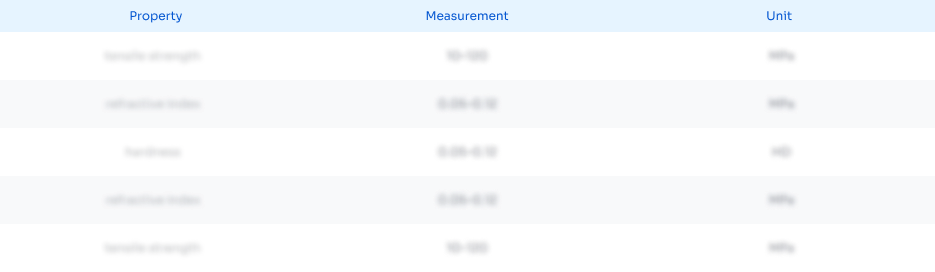
Abstract
Description
Claims
Application Information

- R&D Engineer
- R&D Manager
- IP Professional
- Industry Leading Data Capabilities
- Powerful AI technology
- Patent DNA Extraction
Browse by: Latest US Patents, China's latest patents, Technical Efficacy Thesaurus, Application Domain, Technology Topic, Popular Technical Reports.
© 2024 PatSnap. All rights reserved.Legal|Privacy policy|Modern Slavery Act Transparency Statement|Sitemap|About US| Contact US: help@patsnap.com