C4 alkylation catalyst and method for preparing high-octane gasoline through C4 alkylation
A high-octane gasoline and carbon tetraalkyl technology, which is applied in catalyst activation/preparation, physical/chemical process catalysts, molecular sieve catalysts, etc., can solve the problems of increasing catalyst costs and improve activity and anti-carbon deposition performance , Strong anti-carbon deposition ability, high dispersion effect
- Summary
- Abstract
- Description
- Claims
- Application Information
AI Technical Summary
Problems solved by technology
Method used
Image
Examples
Embodiment 1
[0028] (1) Preparation of directing agent
[0029] Add 2.3g of sodium hydroxide, 1.4g of pseudo-boehmite and 11.9g of deionized water into the beaker, stir to dissolve completely, add 12.6g of sodium silicate solution, stir vigorously, seal and age for 24 hours to obtain a directing agent solution ;
[0030] (2) Preparation of Mo modified Y molecular sieve
[0031] Add 6.3g of molybdenum cyclohexanoate into 50.0g of cyclohexane, and stir evenly after dissolving to form an organic solution containing molybdenum;
[0032] 63.7g sodium hydroxide, 82.9g sodium aluminate and 890g silica sol (35wt% SiO 2 content) into 2000g deionized water in turn, and stirred at room temperature until a uniform sol solution was formed;
[0033] Add the prepared directing agent solution to the sol solution, stir evenly, add the molybdenum-containing organic solution, and continue stirring until a uniform sol solution is formed;
[0034] Transfer the above sol solution into a hydrothermal crystal...
Embodiment 3
[0068] This example provides a preparation method for in-situ synthesis of Mo-modified Y molecular sieve and its application example in C4 alkylation reaction:
[0069] Add 2.3g of sodium hydroxide, 1.35g of pseudo-boehmite and 11.9g of deionized water into the beaker, stir to dissolve completely, add 12.6g of sodium silicate solution, stir vigorously, seal and age for 24 hours to obtain a directing agent solution ;
[0070] Add 6.6g of molybdenum cyclohexanoate into 68.5g of cyclohexane, stir evenly to form molybdenum-containing organic solution after dissolving completely;
[0071] With 76.9g sodium hydroxide, 105.6g pseudo-boehmite and 900g water glass solution (30wt%SiO 2 content) into 2100g deionized water in turn, and stirred at room temperature until a uniform sol solution was formed;
[0072] Add the prepared directing agent to the sol solution, stir evenly, then add the molybdenum-containing organic solution, and continue stirring until a uniform sol solution is for...
Embodiment 4
[0087] This example provides a preparation method for in-situ synthesis of Mo-modified Y molecular sieve and its application example in C4 alkylation reaction:
[0088] Add 2.3g of sodium hydroxide, 1.35g of pseudo-boehmite and 11.9g of deionized water into the beaker, stir to dissolve completely, add 12.6g of sodium silicate solution, stir vigorously, seal and age for 24 hours to obtain a directing agent solution ;
[0089] Add 9.0g of molybdenum octadecyl salicylate into 80.0g of cyclohexane, and stir evenly after dissolving to form an organic solution containing molybdenum;
[0090] 51.3g sodium hydroxide, 89.8g sodium aluminate, and 700g silica sol (35wt% SiO 2 Content) was added to 2500g deionized water in turn, and stirred at room temperature until a uniform sol solution was formed;
[0091] Add the prepared directing agent to the sol solution, stir evenly, then add the molybdenum-containing organic solution, and continue stirring until a uniform sol solution is formed...
PUM
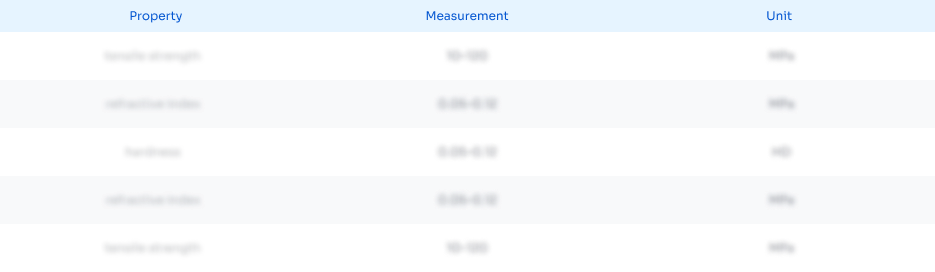
Abstract
Description
Claims
Application Information

- Generate Ideas
- Intellectual Property
- Life Sciences
- Materials
- Tech Scout
- Unparalleled Data Quality
- Higher Quality Content
- 60% Fewer Hallucinations
Browse by: Latest US Patents, China's latest patents, Technical Efficacy Thesaurus, Application Domain, Technology Topic, Popular Technical Reports.
© 2025 PatSnap. All rights reserved.Legal|Privacy policy|Modern Slavery Act Transparency Statement|Sitemap|About US| Contact US: help@patsnap.com