Polymer composite material with high gas barrier property
A composite material and polymer technology, which is applied in the field of polymer composite materials, can solve problems such as blasting of the outer protective layer, collapse of the outer pressure layer, and acceleration of the failure rate of the flexible riser, so as to achieve the effect of improving the barrier performance
- Summary
- Abstract
- Description
- Claims
- Application Information
AI Technical Summary
Problems solved by technology
Method used
Image
Examples
Embodiment 1
[0042] Step 01: Oxidative modification of graphene by the Hummers method to obtain graphene oxide;
[0043] Step 02: Grind the obtained graphene oxide and dry it at 0°C for 24 hours; use a low-energy ball mill (500r / min) to mechanically mix high-density polyethylene (brand 5000S) and graphene oxide in a certain proportion, and the mixing time is 1 hour ;
[0044] Step 03: Dry the mechanically mixed high-density polyethylene and graphene oxide at 70°C for 24 hours, and then granulate through twin-screw extrusion; the barrel temperatures of the twin-screw extruders are: zone 1, 150°C, zone 2, 190°C , Zone 3, 190°C, Zone 4, 190°C, Zone 5, 150°C
[0045] Step 04: Use a flat vulcanizer to prepare a 500um sheet; the pressure of the flat vulcanizer to press the sheet is 30MPa, hot press for 5 minutes, and then turn to room temperature and press at 25°C for 10 minutes;
[0046] Step 05: Conduct CO 2 and CH 4 Permeability test. (The prepared samples were tested for CO by the delay...
Embodiment 2
[0051] Step 01: Oxidative modification of graphene by the Hummers method to obtain graphene oxide;
[0052] Step 02: Grind the obtained graphene oxide and dry it at 0°C for 24 hours; use a low-energy ball mill (500r / min) to mechanically mix high-density polyethylene (brand 8008H) and graphene oxide in a certain proportion, and the mixing time is 1 hour ;
[0053] Step 03: Dry the mechanically mixed high-density polyethylene and graphene oxide at 70°C for 24 hours, and then granulate through twin-screw extrusion; the barrel temperatures of the twin-screw extruders are: zone 1, 150°C, zone 2, 190°C , Zone 3, 190°C, Zone 4, 190°C, Zone 5, 150°C
[0054] Step 04: Use a flat vulcanizer to prepare a 500um sheet; the pressure of the flat vulcanizer to press the sheet is 30MPa, hot press for 5 minutes, and then turn to room temperature and press at 25°C for 10 minutes;
[0055] Step 05: Conduct CO 2 and CH 4 Permeability test.
[0056] Table 3 shows the performance parameters of ...
Embodiment 3
[0060] Step 01: Oxidative modification of graphene by the Hummers method to obtain graphene oxide;
[0061] Step 02: Grind the obtained graphene oxide and dry it at 0°C for 24 hours; use a low-energy ball mill (500r / min) to mechanically mix high-density polyethylene (brand 2200J) and graphene oxide in a certain proportion, and the mixing time is 1 hour ;
[0062] Step 03: Dry the mechanically mixed high-density polyethylene and graphene oxide at 70°C for 24 hours, and then granulate through twin-screw extrusion; the barrel temperatures of the twin-screw extruders are: zone 1, 150°C, zone 2, 190°C , Zone 3, 190°C, Zone 4, 190°C, Zone 5, 150°C
[0063] Step 04: Use a flat vulcanizer to prepare a 500um sheet; the pressure of the flat vulcanizer to press the sheet is 30MPa, hot press for 5 minutes, and then turn to room temperature and press at 25°C for 10 minutes;
[0064] Step 05: Conduct CO 2 and CH 4 Permeability test.
[0065] Table 4 is the performance parameter of the ...
PUM
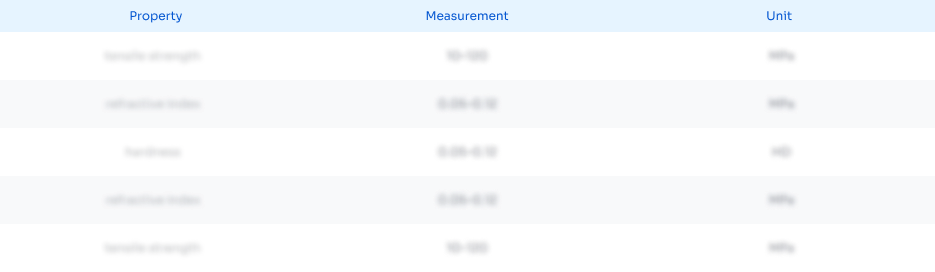
Abstract
Description
Claims
Application Information

- R&D
- Intellectual Property
- Life Sciences
- Materials
- Tech Scout
- Unparalleled Data Quality
- Higher Quality Content
- 60% Fewer Hallucinations
Browse by: Latest US Patents, China's latest patents, Technical Efficacy Thesaurus, Application Domain, Technology Topic, Popular Technical Reports.
© 2025 PatSnap. All rights reserved.Legal|Privacy policy|Modern Slavery Act Transparency Statement|Sitemap|About US| Contact US: help@patsnap.com