Manufacturing method of universal ball cage holder
A manufacturing method and cage technology, used in metal processing equipment, transportation and packaging, etc., can solve the high requirements of mold thermal stability, high temperature strength, hardness and impact toughness, thermal fatigue resistance, wear resistance and processing performance. The problems of low utilization rate of ordinary forging materials and difficulty in realizing full utilization of materials have achieved the effects of low processing difficulty and low processing cost, elimination of excess capacity and high yield rate.
- Summary
- Abstract
- Description
- Claims
- Application Information
AI Technical Summary
Problems solved by technology
Method used
Image
Examples
Embodiment 1
[0039] Such as Figure 1 to Figure 4 As shown, the manufacturing method of the universal ball cage provided by the present invention comprises the following steps:
[0040] A Mix ASTM 86 series low alloy powder and binder according to the weight ratio (87.7~91.2)%: (8.8~12.3)% to obtain low alloy steel feed; among them, the D90 size of ASTM 86 series low alloy powder is 10 ~55μm, the main component of the binder is polyoxymethylene (POM), the mass proportion of POM in the binder is 80~95%, the binder also contains lubricants, surfactants, antioxidants, plasticizers, compatibilizers , high-temperature shape-preserving agent and other additives, these additives are made of polymer materials, and the mixing time is 0.5~2h.
[0041] B. The feed material is made into columnar particles of φ3*5mm through banburying and granulation; when banburying, use an internal mixer to mix, and heat and pressurize the feed material. The banburying temperature is 170~180°C. The pressure is 0.35...
Embodiment 2
[0053] Embodiment two is basically the same as embodiment one, the difference is that, as Figure 5 and Figure 6 As shown, the size of the molded body in Example 2 is scaled up according to the size of the split body after the universal ball cage is divided into half in the radial direction, and the surfaces of the two molded bodies used for combination are equipped with Concave-convex snap-fit structure.
Embodiment 3
[0055] Embodiment three is basically the same as embodiment one, the difference is that, as Figure 7 and Figure 8 As shown, the green body in Example 3 includes a molded body and a mold core. The size of the molded body is scaled up according to the size of the entire universal ball cage. The mold core is made of polyoxymethylene material through injection molding process. The mold core It is completely removed by catalytic degreasing in step D without extraction.
[0056] Using polyoxymethylene material to make the mold core can not only form a complete universal ball cage molded body at one time, so that the final universal ball cage has high precision and no hidden process risks, but also can be removed simultaneously by catalytic degreasing to avoid The extraction action of the mold is simple and convenient to operate. Compared with the traditional mold, the mold core and the molded body both contain polyoxymethylene components. The surface finish on the inner wall of ...
PUM
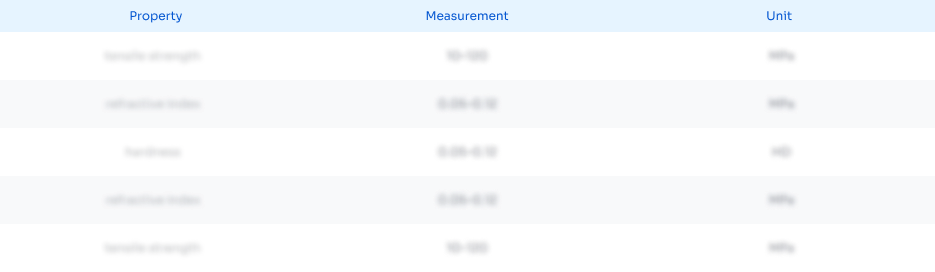
Abstract
Description
Claims
Application Information

- R&D
- Intellectual Property
- Life Sciences
- Materials
- Tech Scout
- Unparalleled Data Quality
- Higher Quality Content
- 60% Fewer Hallucinations
Browse by: Latest US Patents, China's latest patents, Technical Efficacy Thesaurus, Application Domain, Technology Topic, Popular Technical Reports.
© 2025 PatSnap. All rights reserved.Legal|Privacy policy|Modern Slavery Act Transparency Statement|Sitemap|About US| Contact US: help@patsnap.com