Hydrogenation catalyst with high denitrification activity
A hydrogenation catalyst and catalyst technology are applied in the field of oil hydrogenation, which can solve the problem of low denitrification activity, and achieve the effects of improving hydrogenation activity, reducing sulfidation temperature, and improving hydrogenation denitrification activity.
- Summary
- Abstract
- Description
- Claims
- Application Information
AI Technical Summary
Problems solved by technology
Method used
Image
Examples
Embodiment 1
[0034] (1) Add 1L of deionized water into the reaction tank as the bottom liquid, put 1L of the mixed solution of aluminum sulfate and nickel sulfate and 1L of sodium hydroxide solution into the raw material tank respectively, and control the temperature of the reaction tank at 60°C. The aluminum sulfate solution was injected into the reaction tank at a rate of 10 mL / min, while the sodium hydroxide solution was injected and the rate was adjusted to keep the pH value of the reaction tank solution constant at 8.0, and the neutralization was completed after 120 min. In the reaction tank at a constant temperature of 85°C and a constant pH value of 8.5, aged for 5 hours, then washed with deionized water for 3 times, filtered, dried the filter cake at 60°C for 3 hours, and then dried at 110°C for 5 hours to obtain modified alumina Powder. Based on the modified alumina powder, the mass fraction of nickel oxide is 5.0%, and the rest is alumina.
[0035] (2) Mix the modified alumina pow...
Embodiment 2
[0039] (1) Add 1L of deionized water into the reaction tank as the bottom liquid, put 1L of the mixed solution of aluminum sulfate and nickel sulfate and 1L of sodium hydroxide solution into the raw material tank respectively, and control the temperature of the reaction tank at 60°C. The aluminum sulfate solution was injected into the reaction tank at a rate of 12 mL / min, while the sodium hydroxide solution was injected and the rate was adjusted to keep the pH value of the reaction tank solution constant at 8.5, and the neutralization was completed after 120 min. In the reaction tank at a constant 80°C and a constant pH value of 9.0, aged for 5 hours, then washed with deionized water for 3 times, filtered, dried the filter cake at 65°C for 5 hours, and then dried at 120°C for 3 hours to obtain modified alumina Powder. Based on the modified alumina powder, the mass fraction of nickel oxide is 6.0%, and the rest is alumina.
[0040] (2) Mix the modified alumina powder prepared ...
Embodiment 3
[0044] (1) Add 1L of deionized water into the reaction tank as the bottom liquid, put 1L of the mixed solution of aluminum sulfate and cobalt sulfate and 1L of sodium metaaluminate solution into the raw material tank respectively, and control the temperature of the reaction tank at 60°C. The aluminum sulfate solution was injected into the reaction tank at a rate of 12 mL / min, while the sodium hydroxide solution was injected and the rate was adjusted to keep the pH value of the reaction tank solution constant at 9.0, and the neutralization was completed after 120 min. In the reaction tank at a constant temperature of 85°C and a constant pH value of 9.0, aged for 4 hours, then washed with deionized water for 3 times, filtered, dried the filter cake at 70°C for 5 hours, and then dried at 120°C for 3 hours to obtain modified alumina Powder. Based on the modified alumina powder, the mass fraction of cobalt oxide is 6.0%, and the rest is alumina.
[0045] (2) Mix the modified alumi...
PUM
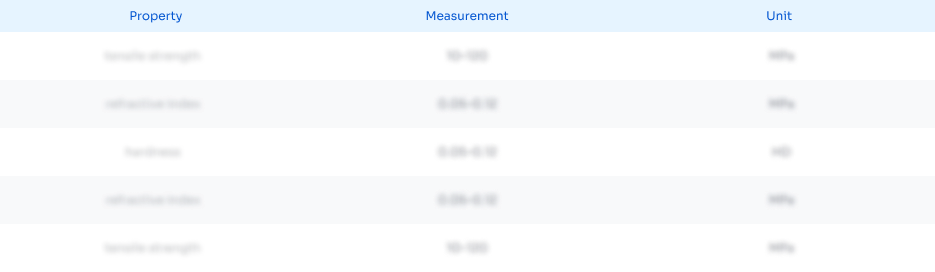
Abstract
Description
Claims
Application Information

- R&D Engineer
- R&D Manager
- IP Professional
- Industry Leading Data Capabilities
- Powerful AI technology
- Patent DNA Extraction
Browse by: Latest US Patents, China's latest patents, Technical Efficacy Thesaurus, Application Domain, Technology Topic, Popular Technical Reports.
© 2024 PatSnap. All rights reserved.Legal|Privacy policy|Modern Slavery Act Transparency Statement|Sitemap|About US| Contact US: help@patsnap.com