Catalyst grading process for reducing polycyclic aromatic hydrocarbon in diesel oil
A polycyclic aromatic hydrocarbon and catalyst technology, applied in the field of catalyst grading process, can solve the problems of affecting catalyst activity, incomplete sulfuration of molybdenum and tungsten, and high hydrogenation activity
- Summary
- Abstract
- Description
- Claims
- Application Information
AI Technical Summary
Problems solved by technology
Method used
Image
Examples
Embodiment 1
[0034] Adjust the ammonium heptamolybdate with ammonia water until it is completely dissolved, prepare an impregnating solution with a concentration of 0.12g / mL, then impregnate an equal volume on the alumina carrier, and dry at 120°C for 3h. Then use 1.5% H 2 The hydrogen of S is vulcanized, the vulcanization temperature is 360°C, the vulcanization pressure is 4.5MPa, the vulcanization time is 6h, and then in N 2 atmosphere down to room temperature, MoS 2 / Al 2 o 3 .
[0035] Dissolve cobalt nitrate in deionized water to prepare an impregnation solution with a concentration of 0.13g / mL, and impregnate MoS with equal volume 2 / Al 2 o 3 , then in N 2 Under the atmosphere, dry at 90°C for 4h, and bake at 320°C for 3h to obtain MoS 2 -CoO / Al 2 o 3 Catalyst C1-1.
Embodiment 2
[0037] Adjust the ammonium heptamolybdate with ammonia water until it is completely dissolved, prepare an impregnating solution with a concentration of 0.12g / mL, then impregnate an equal volume on the alumina carrier, and dry at 120°C for 3h. Then use dimethyl disulfide for vulcanization treatment, the vulcanization temperature is 330 ° C, the vulcanization pressure is 4.5 MPa, the vulcanization time is 6 hours, and then in N 2 atmosphere down to room temperature, MoS 2 / Al 2 o 3 .
[0038] Dissolve nickel nitrate in deionized water, prepare an impregnation solution with a concentration of 0.12g / mL, and impregnate MoS with equal volume 2 / Al 2 o 3 , then in N 2 Under the atmosphere, dry at 80°C for 4h, and bake at 300°C for 3h to obtain MoS 2 -NiO / Al 2 o 3 Catalyst C1-2.
Embodiment 3
[0040] Adjust the ammonium heptamolybdate with ammonia water until it is completely dissolved, prepare an impregnating solution with a concentration of 0.12g / mL, then impregnate an equal volume on the alumina carrier, and dry at 120°C for 3h. Then use 1.5% H 2 The hydrogen of S is vulcanized, the vulcanization temperature is 350°C, the vulcanization pressure is 4.5MPa, the vulcanization time is 6h, and then in N 2 atmosphere down to room temperature, MoS 2 / Al 2 o 3 .
[0041] Dissolve nickel nitrate and cobalt nitrate in deionized water, prepare an impregnation solution with a concentration of 0.12g / mL, and impregnate MoS with equal volume 2 / Al 2 o 3 , then in N 2 Under the atmosphere, dry at 60°C for 4h, and bake at 320°C for 3h to obtain MoS 2 -NiO-CoO / Al 2 o 3 Catalysts C1-3.
PUM
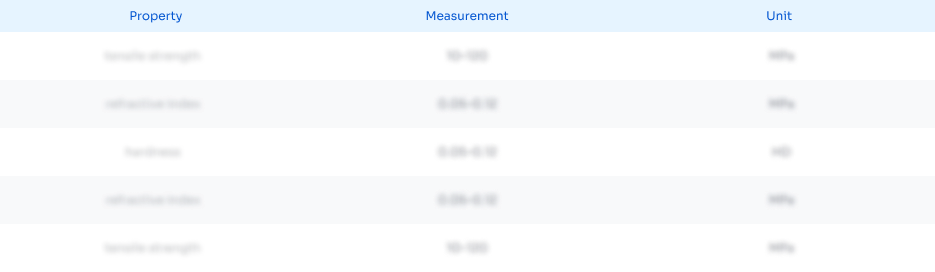
Abstract
Description
Claims
Application Information

- R&D Engineer
- R&D Manager
- IP Professional
- Industry Leading Data Capabilities
- Powerful AI technology
- Patent DNA Extraction
Browse by: Latest US Patents, China's latest patents, Technical Efficacy Thesaurus, Application Domain, Technology Topic.
© 2024 PatSnap. All rights reserved.Legal|Privacy policy|Modern Slavery Act Transparency Statement|Sitemap