Preparation method of silicone rubber electromagnetic shielding composite material with three-layer structure
An electromagnetic shielding and composite material technology, which is applied in the fields of magnetic field/electric field shielding, rubber layered products, chemical instruments and methods, etc., can solve the problems of complex preparation process, large amount of chemical solvents, and high cost, and achieves simple process and simple preparation method. Effective, cost-saving effect
- Summary
- Abstract
- Description
- Claims
- Application Information
AI Technical Summary
Problems solved by technology
Method used
Image
Examples
preparation example Construction
[0022] A kind of silicone rubber electromagnetic shielding composite material with three-layer structure and preparation method thereof of the present invention, specifically comprise the following steps:
[0023] A magnetic shielding composite comprising the steps of:
[0024] Step 1, mix 100 parts by weight of raw silicone rubber (MVQ) with 3-10 parts by weight of 2,5-dimethyl-2,5-bis-hexane (DBPH), 3-7 parts by weight of zinc oxide, 3-5 parts by weight of stearic acid and 30-80 parts by weight of white carbon black (WCB) are fully mixed in an internal mixer to obtain a mixed rubber;
[0025] Step 2, use the open mill to roll the mixed rubber to discharge the air bubbles in the mixed rubber, divide the mixed rubber into 60-80g according to the mass, and cut it into 9cm×13cm sheets, put the sheets on the plastic wrap Upper spare, marked as insulating layer;
[0026] Step 3, mix 100 parts by weight of silicone rubber (MVQ) raw rubber MVQ with 3-10 parts by weight of 2,5-dime...
Embodiment 1
[0032] 100 mass parts of MVQ raw rubber, 3 mass parts of DBPH, 3 mass parts of zinc oxide, 3 mass parts of stearic acid, and 30 mass parts of WCB are placed in the internal mixer, and the roller speed is adjusted to 30r / min mixing for 35 minutes; use the open mill to press the mixing rubber roller to discharge the air bubbles in the mixing rubber, cut it into a 9cm×13cm sheet with a mass of 60g, put the sheet on a plastic wrap for later use, and mark it as insulation Floor. Put 100 parts by mass of MVQ raw rubber, 3 parts by mass of DBPH, 3 parts by mass of zinc oxide, 3 parts by mass of stearic acid, 20 parts by mass of CB, and 1 part by mass of GR in an internal mixer, and roll the Adjust the speed to 30r / min and knead for 35min; use the open mill to press the mixed rubber roller to discharge the air bubbles in the mixed rubber, cut it into a 9cm×13cm sheet with a mass of 50g, and mark the sheet as a conductive layer ;Lay the sheets according to the order of conductive lay...
Embodiment 2
[0034] 100 mass parts of MVQ raw rubber, 6 mass parts of DBPH, 5 mass parts of zinc oxide, 4 mass parts of stearic acid, and 50 mass parts of WCB are placed in the mixer, and the roller speed is adjusted to 30r / min mixing 35min. Use an open mill to roll the mixed rubber to discharge the air bubbles in the mixed rubber, cut it into a 9cm×13cm sheet with a mass of 80g, put the sheet on a plastic wrap and mark it as an insulating layer. Put 100 parts by mass of MVQ raw rubber, 5 parts by mass of DBPH, 5 parts by mass of zinc oxide, 4 parts by mass of stearic acid, 45 parts by mass of CB, and 5 parts by mass of GR in a mixer, and roll the Adjust the speed to 30r / min and knead for 35min. Use an open mill to roll the mixed rubber to discharge the air bubbles in the mixed rubber, cut it into a 9cm×13cm sheet with a mass of 50g, and mark the sheet as a conductive layer. Laminate the sheets sequentially according to the conductive layer-insulating layer-conductive layer, and roll th...
PUM
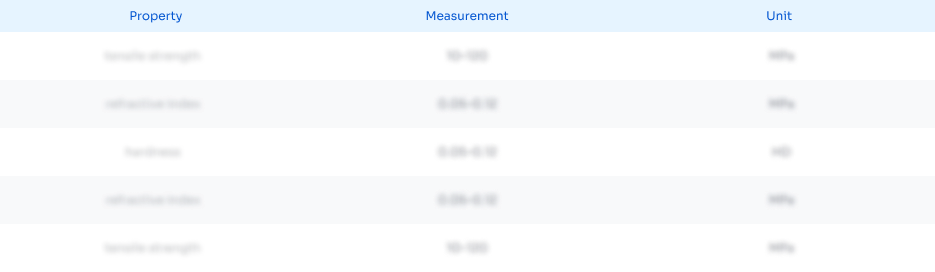
Abstract
Description
Claims
Application Information

- Generate Ideas
- Intellectual Property
- Life Sciences
- Materials
- Tech Scout
- Unparalleled Data Quality
- Higher Quality Content
- 60% Fewer Hallucinations
Browse by: Latest US Patents, China's latest patents, Technical Efficacy Thesaurus, Application Domain, Technology Topic, Popular Technical Reports.
© 2025 PatSnap. All rights reserved.Legal|Privacy policy|Modern Slavery Act Transparency Statement|Sitemap|About US| Contact US: help@patsnap.com