Nano cutter coating and preparation method thereof
A nano-coating and cutting tool technology, applied in coatings, metal material coating processes, manufacturing tools, etc., to achieve the effects of improving the bonding strength of coatings, enhancing mechanical scarfing, and reducing radial displacement
- Summary
- Abstract
- Description
- Claims
- Application Information
AI Technical Summary
Problems solved by technology
Method used
Image
Examples
Embodiment 1
[0039] refer to figure 2 Shown, a kind of nano cutting tool coating and preparation method thereof, concrete steps are as follows:
[0040] The base material of the tool is WC / Co cemented carbide, and the multi-scale bionic structure design of the tool coating is carried out in imitation of the microstructure of C. squamiferum, that is, three micron-scale layers are formed by sputtering target particle gradient growth, layer growth, and co-growth Functionally graded coatings, and introduce nanoscale corrugated structures between the interfaces of each layer to regulate the bonding strength between layers, so that the tool coating as a whole presents a "hard-tough-hard" three-layer composite structure. Its specific preparation process steps are as follows:
[0041] (1) Substrate grinding and polishing, ultrasonic cleaning: Prepare metallographic samples on the surface of the tool substrate on an automatic metallographic grinding machine, then use absolute ethanol to grind wit...
Embodiment 2
[0048] refer to figure 2 Shown, a kind of nano cutting tool coating and preparation method thereof, concrete steps are as follows:
[0049] The base material of the cutting tool is high-speed steel, and the multi-scale bionic structure design of the cutting tool coating is carried out in imitation of the microstructure of C. squamiferum, that is, a three-layer functionally graded coating at the micron scale is formed by sputtering target particle gradient growth, layer growth, and co-growth , and introduce a nanoscale corrugated structure between the interfaces of each layer to regulate the bonding strength between layers, so that the tool coating as a whole presents a "hard-tough-hard" three-layer composite structure. Its specific preparation process steps are as follows:
[0050] (1) Substrate grinding and polishing, ultrasonic cleaning: Prepare metallographic samples on the surface of the tool substrate on an automatic metallographic grinding machine, then use absolute et...
PUM
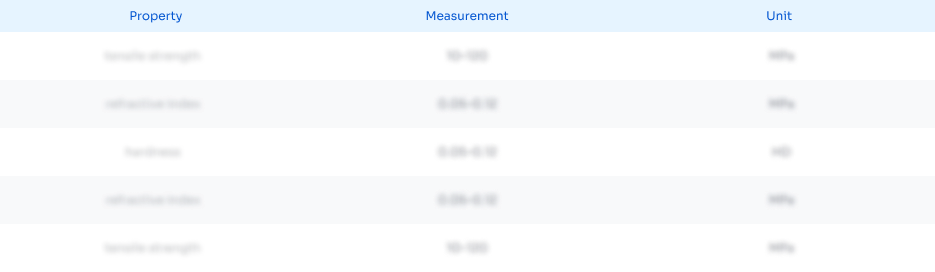
Abstract
Description
Claims
Application Information

- R&D Engineer
- R&D Manager
- IP Professional
- Industry Leading Data Capabilities
- Powerful AI technology
- Patent DNA Extraction
Browse by: Latest US Patents, China's latest patents, Technical Efficacy Thesaurus, Application Domain, Technology Topic, Popular Technical Reports.
© 2024 PatSnap. All rights reserved.Legal|Privacy policy|Modern Slavery Act Transparency Statement|Sitemap|About US| Contact US: help@patsnap.com