Milling machining method for heat-proof layer
A technology of milling processing and heat protection layer, applied in metal processing, metal processing equipment, milling machine equipment, etc., can solve the problems of poor apparent quality, difficult to remove burrs, uneven processing surface, improve accuracy and reduce rework rate , the effect of improving the apparent quality
- Summary
- Abstract
- Description
- Claims
- Application Information
AI Technical Summary
Problems solved by technology
Method used
Image
Examples
Embodiment 2
[0052] This embodiment discloses a milling method for a heat-resistant layer, wherein the weight of dibutyl phthalate is preferably 6 parts, and the weight of triethylenetetramine is preferably 14 parts. In this embodiment In the example, the thickness of the cured layer infiltrated into the processed surface and the heat-proof layer is about 2-3 mm, and it takes 12 hours to cure at room temperature. After heating the cured glue to 80 degrees Celsius, the cured layer takes 4 hours and 10 minutes to cure.
Embodiment 3
[0054] This embodiment discloses a milling method for a heat-resistant layer, wherein the weight parts of dibutyl phthalate is preferably 6 parts, and the weight parts of triethylenetetramine is preferably 13 parts. In this embodiment In the example, the thickness of the cured layer infiltrated into the processing surface and the heat-proof layer is about 2-3mm, and it takes 12.5 hours to cure at room temperature. After heating the cured glue to 80 degrees Celsius, the cured layer takes 4 hours and 16 minutes to cure.
PUM
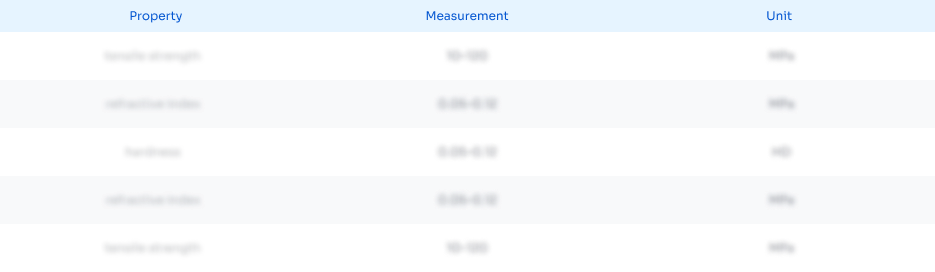
Abstract
Description
Claims
Application Information

- R&D
- Intellectual Property
- Life Sciences
- Materials
- Tech Scout
- Unparalleled Data Quality
- Higher Quality Content
- 60% Fewer Hallucinations
Browse by: Latest US Patents, China's latest patents, Technical Efficacy Thesaurus, Application Domain, Technology Topic, Popular Technical Reports.
© 2025 PatSnap. All rights reserved.Legal|Privacy policy|Modern Slavery Act Transparency Statement|Sitemap|About US| Contact US: help@patsnap.com