Method and system for recovering ammonia from nitrile-containing organic wastewater
A technology for recovering ammonia from organic wastewater, applied in ammonia preparation/separation, chemical instruments and methods, inorganic chemistry, etc., can solve problems such as pipelines affecting the stable operation of devices, and achieve the effect of improving the effect
- Summary
- Abstract
- Description
- Claims
- Application Information
AI Technical Summary
Problems solved by technology
Method used
Image
Examples
Embodiment 1
[0062] 1. Preparation of wet oxidation catalyst
[0063] 1.1 Preparation method of catalyst carrier:
[0064] 20g Ba(NO 3 ) 2 Dissolved in 200mL water to prepare solution A, 160g of TiOSO 4 Dissolve in 2L of water to form solution B. At room temperature and at a stirring speed of 300 rpm, slowly add solution A and ammonia water (ammonia concentration 25-28wt%) into solution B slowly, control the final pH of the solution to 7.0, and continue stirring 2h. After the precipitate was filtered, it was washed three times with 500 mL of deionized water, and then dried at 80° C. for 24 h to obtain the precursor of the catalyst carrier. After mixing 100g of the powdered precursor with 5g of CMC, 10g of nitric acid, and 30g of water evenly, extrude into a strip, dry at room temperature for 48h, and roast at 500°C for 4h to obtain the catalyst carrier.
[0065] 1.2 Preparation method of catalyst
[0066] 0.5g H 2 PtCI 6 It was dissolved in 30 g of water, and 100 g of the catalyst ...
Embodiment 2
[0070] 1. Catalytic wet oxidation catalyst preparation
[0071] 1.1 Preparation method of catalyst carrier:
[0072] 30g Ba(NO 3 ) 2 Dissolved in 200mL water to prepare solution A, 160g of TiOSO 4 Dissolve in 2L of water to form solution B. At room temperature and at a stirring speed of 300 rpm, slowly add solution A and ammonia water (ammonia concentration 25-28wt%) into solution B slowly, control the final pH of the solution to 9.0, and continue stirring 2h, a precipitate formed. After the precipitate was filtered, it was washed three times with 500 mL of deionized water, and then dried at 80° C. for 24 h to obtain the precursor of the catalyst carrier. 100g of the powdered catalyst carrier precursor was uniformly mixed with 5g of CMC, 10g of sulfuric acid, and 30g of water, extruded, dried at room temperature for 48 hours, and calcined at 500°C for 4 hours to obtain the catalyst carrier.
[0073] 1.2 Preparation method of catalyst
[0074] 0.5gH 2 PtCl 6 It was diss...
Embodiment 3
[0078] 1. Catalytic wet oxidation catalyst preparation
[0079] 1.1 Preparation method of catalyst carrier:
[0080] 30g Ba(NO 3 ) 2 Dissolved in 200mL water to prepare solution A, 160g of TiOSO 4 Dissolve in 2L of water to form solution B. At room temperature and at a stirring speed of 300 rpm, slowly add solution A and 1M sodium carbonate solution dropwise to solution B respectively, control the final pH of the solution to 9.0, and continue stirring for 2 hours to form a precipitate thing. After the precipitate was filtered, it was washed three times with 500 mL of deionized water, and then dried at 80° C. for 24 h to obtain the precursor of the catalyst carrier. 100g of the powdered catalyst carrier precursor was uniformly mixed with 5g of CMC, 10g of sulfuric acid, and 30g of water, extruded, dried at room temperature for 48 hours, and calcined at 550°C for 4 hours to obtain the catalyst carrier.
[0081] 1.2 Preparation method of catalyst
[0082] 0.5gH 2 PtCl 6 I...
PUM
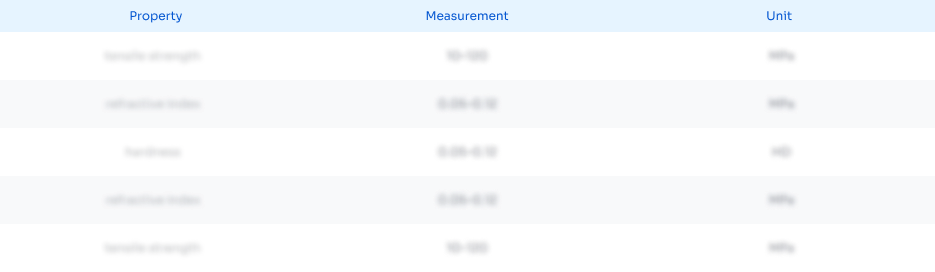
Abstract
Description
Claims
Application Information

- R&D
- Intellectual Property
- Life Sciences
- Materials
- Tech Scout
- Unparalleled Data Quality
- Higher Quality Content
- 60% Fewer Hallucinations
Browse by: Latest US Patents, China's latest patents, Technical Efficacy Thesaurus, Application Domain, Technology Topic, Popular Technical Reports.
© 2025 PatSnap. All rights reserved.Legal|Privacy policy|Modern Slavery Act Transparency Statement|Sitemap|About US| Contact US: help@patsnap.com