Triangular shaft sleeve machining method
A processing method and triangular shaft technology, applied in the direction of shaft couplings, rigid shaft couplings, mechanical equipment, etc., can solve the problem of low alignment accuracy, large vibration of the whole machine, and inability to ensure the coaxiality of the inner hole and the outer circle degree requirements etc.
- Summary
- Abstract
- Description
- Claims
- Application Information
AI Technical Summary
Problems solved by technology
Method used
Image
Examples
Embodiment Construction
[0050] Embodiments of the present invention are described in detail below, examples of which are shown in the drawings, wherein the same or similar reference numerals designate the same or similar elements or elements having the same or similar functions throughout. The embodiments described below by referring to the figures are exemplary and are intended to explain the present invention and should not be construed as limiting the present invention.
[0051] see Figure 1 to Figure 14 , the present invention provides a processing method of a triangular bushing: the triangular bushing 1 includes a special-shaped hole 11 and a circular hole 12, the circular hole 12 is located in the middle of the special-shaped hole 11, here the special-shaped hole 11 is Taking the triangular hole as an example, the processing method of the triangular bushing 1 includes:
[0052] S101 obtains the test rod and detects it;
[0053] The specific steps are:
[0054] S201 illuminates the surface o...
PUM
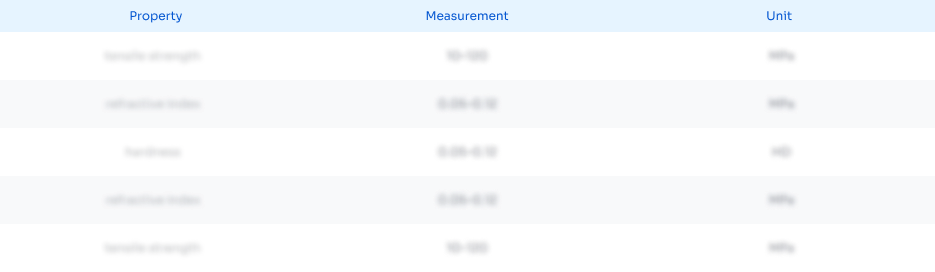
Abstract
Description
Claims
Application Information

- R&D
- Intellectual Property
- Life Sciences
- Materials
- Tech Scout
- Unparalleled Data Quality
- Higher Quality Content
- 60% Fewer Hallucinations
Browse by: Latest US Patents, China's latest patents, Technical Efficacy Thesaurus, Application Domain, Technology Topic, Popular Technical Reports.
© 2025 PatSnap. All rights reserved.Legal|Privacy policy|Modern Slavery Act Transparency Statement|Sitemap|About US| Contact US: help@patsnap.com