Method for increasing number of continuous drawing furnaces of sulfur-containing gear steel
A technology of gear steel and continuous drawing, which is applied in the field of metallurgy, can solve the problems of stopper rod rising, shutdown, and flow loss, and achieve the goals of improving the pass rate of cast billets and molten steel yield, broad application prospects, and increasing the number of continuous drawing furnaces Effect
- Summary
- Abstract
- Description
- Claims
- Application Information
AI Technical Summary
Problems solved by technology
Method used
Image
Examples
Embodiment 1
[0037] A method of increasing the number of continuous drawing furnaces of sulfur-containing gear steel in this embodiment comprises the following steps:
[0038] (1) Converter smelting: Converter smelting end point C: 0.08%, P: 0.012%, tapping temperature 1636°C, adding 100kg of aluminum block and 400kg of synthetic slag when tapping 1 / 3 (synthetic slag composition: CaO: 48% , SiO 2 : 9%, Al 2 o 3 : 36%, MgO: 7%); oxygen content in steel 35 ppm; tapping time 4min15s, ladle argon blowing time 4min30s, the alloy material on the surface of the slag layer is not agglomerated; the ladle headroom for converter tapping is 350mm, and the amount of slag is 3kg / ton of steel;
[0039] (2) LF refining: micro positive pressure operation throughout the whole process, the damper opening of the side suction in the early stage of refining is controlled at 72%, and the damper opening is controlled at 31% in the middle and later stages; 7.5kg / t of lime is added during the heating process, ...
Embodiment 2
[0044] (1) Converter smelting: Converter smelting end point C: 0.09%, P: 0.013%, tapping temperature 1631°C, adding 120kg of aluminum block and 400kg of synthetic slag when tapping 1 / 3 (synthetic slag composition: CaO: 42% , SiO 2 : 10%, Al 2 o 3 : 40%, MgO: 8%); the oxygen content in the steel is 40 ppm; the tapping time is 4min21s, the ladle argon blowing time is 3min26s, the alloy material on the surface of the slag layer is not lumpy; the ladle headroom for converter tapping is 300mm; 3.5kg / ton of steel;
[0045] (2) LF refining: micro positive pressure operation throughout the whole process, the damper opening of side suction is controlled at 80% in the early stage of refining; the damper opening is controlled at 26% in the middle and late stages; 9.8kg / t of lime is added during the heating process, and silicon carbide is added in total Amount of 0.3kg / t, refining final slag composition: TFe 0.56%, CaO 54.8%, SiO 2 15%, Al 2 o 3 22.6%, MgO 7.04%, heat storage of th...
Embodiment 3
[0050] (1) Converter smelting: Converter smelting end point C: 0.10%, P: 0.014%, tapping temperature 1633°C, adding 150kg of aluminum block and 400kg of synthetic slag when tapping 1 / 3 (synthetic slag composition: CaO: 55% , SiO 2 : 3%, Al 2 o 3 : 32%, MgO: 10%); oxygen content in steel 26 ppm; tapping time 5min13s, ladle argon blowing time 3min20s, alloy material on the surface of slag layer is not agglomerated; converter tapping ladle clearance is 400mm, slag amount 2kg / ton of steel;
[0051] (2) LF refining: micro positive pressure operation throughout the whole process, the damper opening of the side suction in the early refining is controlled at 85%; the damper opening is controlled at 38% in the middle and late stages; 10.2kg / t of lime is added during the heating process, and silicon carbide is added in total Amount of 0.30㎏ / t, refining final slag composition: TFe 0.5%, CaO 55.5%, SiO 2 13%, Al 2 O3 23%, MgO 8.0%; during the refining process, the ladle heat is st...
PUM
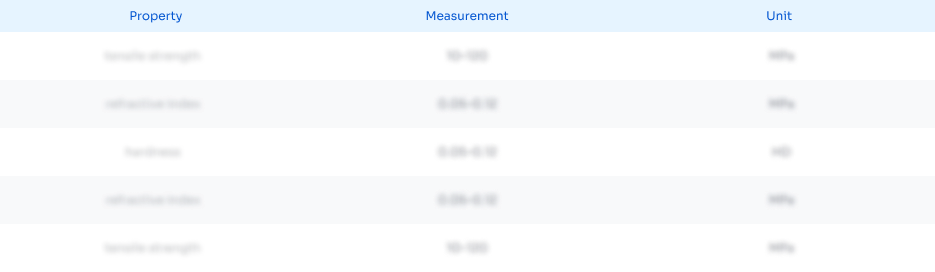
Abstract
Description
Claims
Application Information

- R&D Engineer
- R&D Manager
- IP Professional
- Industry Leading Data Capabilities
- Powerful AI technology
- Patent DNA Extraction
Browse by: Latest US Patents, China's latest patents, Technical Efficacy Thesaurus, Application Domain, Technology Topic, Popular Technical Reports.
© 2024 PatSnap. All rights reserved.Legal|Privacy policy|Modern Slavery Act Transparency Statement|Sitemap|About US| Contact US: help@patsnap.com