Method for preparing cementing material from bauxite mill tailings
A technology of cementitious materials and bauxite, which is applied in the field of comprehensive utilization of industrial solid waste, can solve the problems of unguaranteed sintering quality, low output, and large limitations
- Summary
- Abstract
- Description
- Claims
- Application Information
AI Technical Summary
Problems solved by technology
Method used
Image
Examples
Embodiment 1
[0041] The invention provides a method for preparing cementitious material from bauxite beneficiation tailings, comprising the following steps:
[0042] 1) Raw material treatment: add red mud to the bauxite beneficiation tailings and dry it to powder, then use it as raw material A, classify and screen coal gangue, crush it, and mix it until the calorific value is equal to 600kJ / kg, Stand-by as raw material B;
[0043] 2) The raw material A and the raw material B are subjected to heat distribution, homogenization, and sedimentation to obtain a mixture, and the dry basis mass ratio of each raw material in the mixture is: raw material B: bauxite beneficiation tailings: red mud=50 : 20:10, and the internal combustion value of the mixture is 250kJ / kg, the fineness is ≤80μm, the sieve residue is ≤15%, and the water content is ≤10%. After mixing with a compulsory mixer for 15 minutes, it is sent to the sinking workshop, and the sinking time is not less than 24 hours;
[0044] 3) Th...
Embodiment 2
[0053] The difference from Example 1 is that in step 4) of Example 2, the calcination temperature is 800° C., and the calcination time is 1 h; in step 6), clinker A, building gypsum B, composite activator and auxiliary agent are pressed The mass ratio is 80:10:9:1 for blending, and in the composite activator, the mass ratio of 42.5 ordinary Portland cement and S95 blast furnace quenched slag is 1:9.
Embodiment 3
[0055] The difference from Example 1 is that in step 4) of Example 3, the calcination temperature is 776°C, and the calcination time is 2h; in step 6), the clinker A, building gypsum B, composite activator and auxiliary agent are pressed The mass ratio is 80:6:13:1 for blending; the composite activator is mixed with sodium hydroxide and water glass, and the mass ratio of sodium hydroxide and water glass is 6:7. Among the auxiliary agents, phosphoric acid The mass ratio of barium to calcium lignosulfonate is 2:8.
PUM
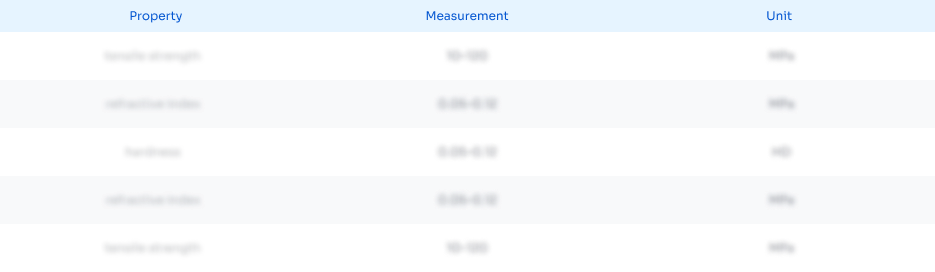
Abstract
Description
Claims
Application Information

- Generate Ideas
- Intellectual Property
- Life Sciences
- Materials
- Tech Scout
- Unparalleled Data Quality
- Higher Quality Content
- 60% Fewer Hallucinations
Browse by: Latest US Patents, China's latest patents, Technical Efficacy Thesaurus, Application Domain, Technology Topic, Popular Technical Reports.
© 2025 PatSnap. All rights reserved.Legal|Privacy policy|Modern Slavery Act Transparency Statement|Sitemap|About US| Contact US: help@patsnap.com