Method for recovering molybdenum from waste nickel-molybdenum catalyst
A catalyst, nickel-molybdenum technology, applied in the field of resource recovery, can solve the problems of many impurities, flue gas pollution, difficulties, etc., and achieve the effects of low reaction temperature, low equipment investment and simple operation
- Summary
- Abstract
- Description
- Claims
- Application Information
AI Technical Summary
Problems solved by technology
Method used
Image
Examples
Embodiment 1
[0037] The waste nickel-molybdenum catalyst selected in this embodiment has a molybdenum mass content of 12.5%, a nickel mass content of 2.4%, an aluminum mass content of 25.4%, and a sulfur mass content of 9.4%, wherein molybdenum mainly exists in the form of molybdenum sulfide, but the crystallinity is relatively poor. Spent catalyst substantially in the form of amorphous alumina.
[0038] The present embodiment provides a kind of method that reclaims molybdenum from waste nickel-molybdenum catalyst, and described method comprises the following steps:
[0039] (1) Use hydrogen peroxide with a mass concentration of 30%, take 40mL, add it to a 500mL three-necked flask, dilute it to 100mL with deionized water, add 20g of spent nickel-molybdenum catalyst, and stir the reaction at 60°C at a stirring speed of 250rpm. 30min to obtain leachate;
[0040] (2) Slowly add ammonia water with a mass concentration of 20% to the leaching solution obtained in step (1), keep the pH at 7.5, r...
Embodiment 2
[0044]The spent nickel-molybdenum catalyst used in this example was washed and deoiled with acetone, and then ground to below 200 mesh. The mass content of molybdenum was measured to be 11.8%, the mass content of nickel was 3.5%, the mass content of sulfur was 10.4%, and the mass content of aluminum was 26.7%.
[0045] The present embodiment provides a kind of method that reclaims molybdenum from waste nickel-molybdenum catalyst, and described method comprises the following steps:
[0046] (1) Take 20 g of finely ground spent catalyst, mix it with 60 mL of deionized water, and put it into a three-necked flask. Add 40 mL of hydrogen peroxide with a mass concentration of 30%, and react at 60°C for 30 minutes to obtain a leaching solution;
[0047] (2) Slowly add ammoniacal liquor with a mass concentration of 20% to the leaching solution obtained in step (1), keep the pH at 7.5, after reacting for 2 hours, filter, and add 30 mL of ammoniacal liquor with a mass concentration of 2...
Embodiment 3
[0050] The only difference between this embodiment and Example 1 is that the addition of hydrogen peroxide in step (1) is 30 mL, (the concentration of hydrogen peroxide after dilution is 9%), and other conditions and parameters are exactly the same as in Example 1.
PUM
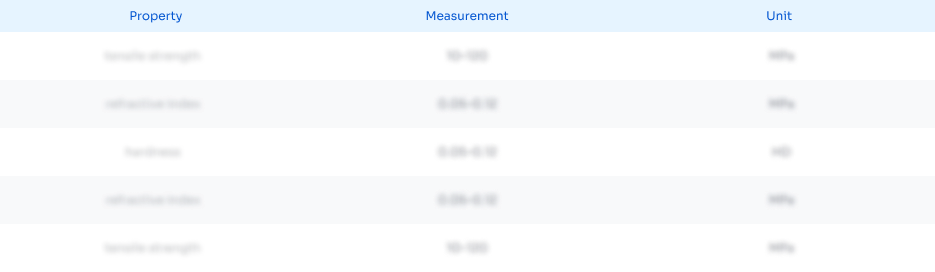
Abstract
Description
Claims
Application Information

- Generate Ideas
- Intellectual Property
- Life Sciences
- Materials
- Tech Scout
- Unparalleled Data Quality
- Higher Quality Content
- 60% Fewer Hallucinations
Browse by: Latest US Patents, China's latest patents, Technical Efficacy Thesaurus, Application Domain, Technology Topic, Popular Technical Reports.
© 2025 PatSnap. All rights reserved.Legal|Privacy policy|Modern Slavery Act Transparency Statement|Sitemap|About US| Contact US: help@patsnap.com