Basalt fiber reinforced high-speed steel rail polishing grinding stone and preparation method thereof
A technology of basalt fiber and grinding stone, which is applied in the direction of grinding/polishing equipment, abrasive materials, grinding devices, etc. It can solve the problems of easy burning of rails, weak grinding ability, and poor self-sharpening, and achieves small wear and smooth grinding The effect of large amount and low grinding temperature
- Summary
- Abstract
- Description
- Claims
- Application Information
AI Technical Summary
Problems solved by technology
Method used
Image
Examples
Embodiment 1
[0022] A kind of basalt fiber reinforced high-speed steel rail grinding stone, its preparation method comprises the following steps:
[0023] 1. Basalt fibers (20 μm in diameter and 260 μm in length) were baked at 250°C for 12 hours, then soaked and etched with 40% NaOH solution for 1 hour, then dried at 80°C for 30 minutes, and finally dried at 80°C for 30 minutes. % silane coupling agent KH550 alcohol solution for 2 hours, and then dried at 80 ° C for 30 minutes to obtain modified basalt fiber.
[0024] 2. Weigh the millstone raw materials by weight: 100 parts of zirconium corundum, 100 parts of brown corundum, 6 parts of pyrite powder, 6 parts of cryolite, 6 parts of barite powder, 6 parts of calcium carbonate, 6 parts of copper powder, liquid 20 parts of epoxy resin, 20 parts of phenolic resin powder and 5 parts of modified basalt fiber.
[0025] 3. Use the vibration method to process the raw materials for 15 minutes, and then ball mill and mix the raw materials for 15 mi...
Embodiment 2
[0029] A kind of basalt fiber reinforced high-speed steel rail grinding stone, its preparation method comprises the following steps:
[0030] 1. Basalt fibers (10 μm in diameter and 40 μm in length) were baked at 200°C for 15 hours, then infiltrated and etched with 20% NaOH solution for 2 hours, then dried at 50°C for 60 minutes, and finally dried at 50°C for 60 minutes. % silane coupling agent KH550 alcohol solution for 1h, and then dried at 50°C for 60min to prepare modified basalt fiber.
[0031] 2. Weigh the millstone raw materials by weight: 80 parts of zirconium corundum, 80 parts of brown corundum, 4 parts of pyrite powder, 4 parts of cryolite, 4 parts of barite powder, 4 parts of calcium carbonate, 4 parts of copper powder, liquid 10 parts of epoxy resin, 10 parts of phenolic resin powder and 1 part of modified basalt fiber.
[0032] 3. Use the vibration method to process the raw materials for 10 minutes, and then ball mill and mix the raw materials for 30 minutes aft...
Embodiment 3
[0036] A kind of basalt fiber reinforced high-speed steel rail grinding stone, its preparation method comprises the following steps:
[0037] 1. Basalt fibers (25 μm in diameter and 325 μm in length) were baked at 500°C for 10 hours, then infiltrated and etched with NaOH solution with a mass fraction of 55% for 0.5 hours, then dried at 100°C for 20 minutes, and finally mixed with a mass fraction of Soak in 5% alcohol solution of silane coupling agent KH550 for 3 hours, then dry at 100°C for 20 minutes to prepare modified basalt fiber.
[0038] 2. Weigh the millstone raw materials by weight: 120 parts of zirconium corundum, 120 parts of brown corundum, 10 parts of pyrite powder, 10 parts of cryolite, 10 parts of barite powder, 10 parts of calcium carbonate, 10 parts of copper powder, liquid 25 parts of epoxy resin, 25 parts of phenolic resin powder and 10 parts of modified basalt fiber.
[0039] 3. Use the vibration method to process the raw materials for 50 minutes, and then ...
PUM
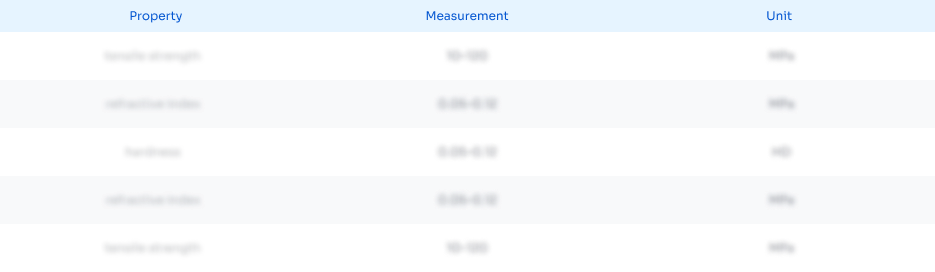
Abstract
Description
Claims
Application Information

- R&D
- Intellectual Property
- Life Sciences
- Materials
- Tech Scout
- Unparalleled Data Quality
- Higher Quality Content
- 60% Fewer Hallucinations
Browse by: Latest US Patents, China's latest patents, Technical Efficacy Thesaurus, Application Domain, Technology Topic, Popular Technical Reports.
© 2025 PatSnap. All rights reserved.Legal|Privacy policy|Modern Slavery Act Transparency Statement|Sitemap|About US| Contact US: help@patsnap.com