Process for improving titanium alloy wire additive manufacturing metallurgical structure
A titanium alloy wire and additive manufacturing technology, which is applied in the field of additive manufacturing, can solve the problems of reducing deformation resistance and not being able to effectively improve the structure of titanium alloys manufactured by additive manufacturing, so as to improve the structure, keep the alloy composition unchanged, and eliminate hydrides Effect
- Summary
- Abstract
- Description
- Claims
- Application Information
AI Technical Summary
Problems solved by technology
Method used
Image
Examples
Embodiment 1
[0053] [Example 1] Pre-position hydrogen + solid solution + printing + post-hydrogen heat treatment process
[0054] 1) The TC4 titanium alloy wire is subjected to hydrogen treatment, and the titanium alloy wire is placed in a tubular hydrogen heat treatment furnace, and the vacuum is evacuated to 1.5*10 -3 Pa, heat at a speed of 10-20°C / min to 700°C-800°C, keep warm for 10-30min, fill in 0.5% hydrogen according to the weight percentage of titanium alloy wire, keep warm for 1-4h, and then heat at 5-15°C / min speed to cool to room temperature, that is, to obtain hydrogen titanium alloy wire.
[0055] 2) The hydrogenated titanium alloy wire is subjected to solution heat treatment. The specific heat treatment process is: put the wire into a heat treatment furnace and heat it to T at a speed of 10-20°C / min. P ℃ (phase transition temperature) + 10 ℃, keep warm for 20-40min, and then quench;
[0056] 3) The solid-dissolved titanium alloy wire is used for additive manufacturing to ...
Embodiment 2
[0059] [Example 2] Pre-positioning hydrogen + printing + dehydrogenation process
[0060] The TC4 titanium alloy wire is subjected to hydrogen treatment, the titanium alloy wire is placed in a tubular hydrogen heat treatment furnace, and the vacuum is evacuated to 1.5*10 -3 Pa, heat at a speed of 10-20°C / min to 700°C-800°C, keep warm for 10-30min, fill in 0.5% hydrogen according to the weight percentage of titanium alloy wire, keep warm for 1-4h, and then heat at 5-15°C / min speed to cool to room temperature, that is, to obtain hydrogenation titanium alloy wire;
[0061] 2) The hydrogenated titanium alloy wire is used for additive manufacturing to obtain titanium alloy workpieces
[0062] Wire feeding process: wire feeding speed: 1~5mm / s, laser power: 1200~5000W;
[0063] 3) Anneal and dehydrogenate the manufactured titanium alloy workpiece; put the titanium alloy workpiece into a vacuum heat treatment furnace, and evacuate to 1.5*10 -3 Pa, heated to 700-800°C at a rate of ...
Embodiment 3
[0064] [Example 3] Pre-positioning hydrogen + solid solution + printing process
[0065] 1) The titanium alloy wire is subjected to hydrogen treatment, and the titanium alloy wire is placed in a tubular hydrogen heat treatment furnace, and the vacuum is evacuated to 1.5*10 -3 Pa, heat at a speed of 10-20°C / min to 700°C-800°C, keep warm for 10-30min, fill in 0.1%-0.8% hydrogen according to the weight percentage of titanium alloy wire, keep warm for 1-4h, and then use 5 Cool to room temperature at a rate of ~15°C / min to obtain a hydrogenated titanium alloy wire.
[0066] 2) The hydrogenated titanium alloy wire is subjected to solution heat treatment. The specific heat treatment process is: put the wire into a heat treatment furnace and heat it to T at a speed of 10-20°C / min. P ℃ (phase transition temperature) + 10 ℃, keep warm for 20-40min, and then quench;
[0067] 3) The solid-dissolved titanium alloy wire is used for additive manufacturing to obtain a titanium alloy workpie...
PUM
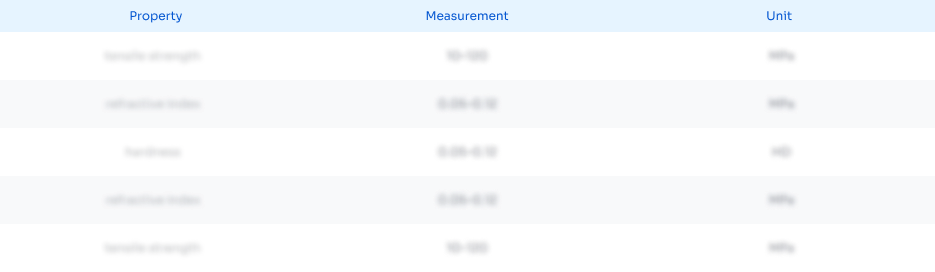
Abstract
Description
Claims
Application Information

- R&D Engineer
- R&D Manager
- IP Professional
- Industry Leading Data Capabilities
- Powerful AI technology
- Patent DNA Extraction
Browse by: Latest US Patents, China's latest patents, Technical Efficacy Thesaurus, Application Domain, Technology Topic, Popular Technical Reports.
© 2024 PatSnap. All rights reserved.Legal|Privacy policy|Modern Slavery Act Transparency Statement|Sitemap|About US| Contact US: help@patsnap.com