Oxidized pellet preparation method and device
A technology for oxidizing pellets and preparation equipment, which is applied in the field of iron and steel metallurgy, and can solve the problem of high equipment cost
- Summary
- Abstract
- Description
- Claims
- Application Information
AI Technical Summary
Problems solved by technology
Method used
Image
Examples
preparation example Construction
[0022] Such as figure 1 As shown, the embodiment of the present invention provides a method for preparing oxidized pellets, including:
[0023] S101, spreading the refractory heat storage balls on the trolley of the belt roaster to form a refractory heat storage ball layer;
[0024] S102, laying green balls on the refractory heat storage ball layer;
[0025] S103. Roasting the green balls on the refractory heat storage ball layer to generate oxidized pellets.
[0026] In the prior art, the oxidized pellets used as finished products are reused and laid on the belt roaster as bottom and edge materials to protect the grates from high temperature damage and prevent powder clogging And bonding grate bars and other purposes. However, due to the limited ability of the oxidized pellets to absorb heat, it is difficult to effectively reduce the temperature of the exhaust air after roasting. The grates still cannot be made of ordinary steel, and the strength of the oxidized pellets wi...
PUM
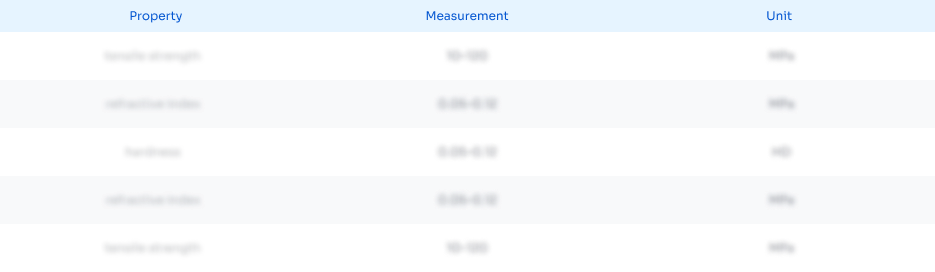
Abstract
Description
Claims
Application Information

- R&D Engineer
- R&D Manager
- IP Professional
- Industry Leading Data Capabilities
- Powerful AI technology
- Patent DNA Extraction
Browse by: Latest US Patents, China's latest patents, Technical Efficacy Thesaurus, Application Domain, Technology Topic, Popular Technical Reports.
© 2024 PatSnap. All rights reserved.Legal|Privacy policy|Modern Slavery Act Transparency Statement|Sitemap|About US| Contact US: help@patsnap.com