Preparation method of pillar porcelain core composite insulator
A composite insulator and pillar porcelain technology, applied in the field of electric porcelain, can solve problems such as edge curling, lower insulation performance of insulators, insufficient anchoring force of high-temperature vulcanized silicone rubber, etc., achieve the effect of reducing thickness and avoiding high temperature
- Summary
- Abstract
- Description
- Claims
- Application Information
AI Technical Summary
Problems solved by technology
Method used
Image
Examples
preparation example Construction
[0029] An aspect of the embodiments of the present invention provides a preparation method of a pillar ceramic core composite insulator, such as Figure 2-4 As shown, the pillar ceramic core composite insulator includes a ceramic core 1, flanges 2 arranged at both ends of the ceramic core 1, and a sheath 3 covering the side wall of the ceramic core 1; The wall is also provided with an umbrella skirt 31 integrally formed therewith; the preparation method includes the following steps:
[0030] 1) Install the flange 2 on both ends of the ceramic core 1;
[0031] 2) Using the outer circular surfaces of the two ends of the ceramic core 1 as the sealing surface of the forming mold, the sheath 3 and the umbrella skirt 31 are integrally formed on the ceramic core 1. During the forming, the forming mold is not compatible with the method. The flange 2 is in contact, and after forming, there is a gap between the inner end face of the flange 2 and the end of the formed sheath 3;
[0032...
Embodiment 1
[0060] Based on e.g. image 3 The shown pillar ceramic core composite insulator includes a ceramic core 1 made of ceramic material, metal flanges 2 arranged at both ends of the ceramic core 1, and a high-temperature vulcanized silicone rubber protective shield covering the side wall of the ceramic core 1. Sleeve 3; the side wall of the sleeve 3 is also provided with an umbrella skirt 31 made of high-temperature vulcanized silicone rubber that is integrally formed with it; prepared according to the following steps:
[0061] 1) Inject cement glue into the cap opening of the flange 2, then insert the end of the ceramic core 1 to complete the glue installation of the flanges 2 at both ends, remove the cement glue overflowing the cap opening of the flange 2, and then put it at room temperature. Continue curing until the cement glue is completely cured;
[0062] 2) as figure 2 As shown, the ceramic core 1 is positioned in the mold of the high-temperature vulcanized silicone rubbe...
Embodiment 2
[0066] The difference between this example and Example 1 is that the mass percentage components of the room temperature vulcanized silicone rubber are: 70kg of hydroxy silicone oil, 10kg of methyl tributyl ketoximosilane, 15kg of fumed silica, particle size of 1-3 microns Aluminum hydroxide 3kg, toner 2kg.
PUM
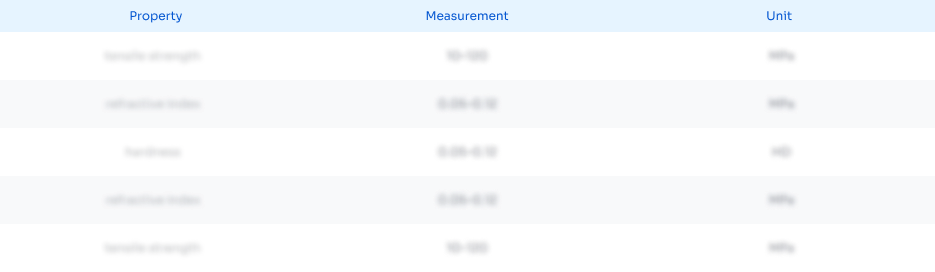
Abstract
Description
Claims
Application Information

- R&D
- Intellectual Property
- Life Sciences
- Materials
- Tech Scout
- Unparalleled Data Quality
- Higher Quality Content
- 60% Fewer Hallucinations
Browse by: Latest US Patents, China's latest patents, Technical Efficacy Thesaurus, Application Domain, Technology Topic, Popular Technical Reports.
© 2025 PatSnap. All rights reserved.Legal|Privacy policy|Modern Slavery Act Transparency Statement|Sitemap|About US| Contact US: help@patsnap.com