Organic silicon electronic pouring sealant capable of being deeply cured and condensed and manufacturing method thereof
A technology of deep curing and manufacturing methods, applied in the direction of adhesives, adhesive additives, polymer adhesive additives, etc., can solve the problems of longer curing time of silicone rubber, affecting product production cycle, limiting application scenarios of condensed silicone rubber, etc. Achieve the effect of improving production efficiency and flexibility, shortening production cycle and reducing hydrolysis
- Summary
- Abstract
- Description
- Claims
- Application Information
AI Technical Summary
Problems solved by technology
Method used
Image
Examples
Embodiment 1
[0034] Put 100 parts of α, ω-dihydroxypolydimethylsiloxane with a viscosity of 1500 mPas at 25±2°C, and 300 parts of aluminum hydroxide, and knead them in a kneader at a temperature of 180°C and a vacuum of -0.08MPa After 3 hours, the base material was obtained after cooling. At room temperature, add 100 parts of the base material, 50 parts of α, ω-dihydroxy polydimethylsiloxane, and 3 parts of high-hydroxyl silicone oil into the planetary mixer, keep the vacuum at -0.08MPa, and stir at a speed of 70rpm. 20 minutes to prepare component A; at room temperature, add 100 parts of ethyl silicate, 0.5 part of γ-aminoethylaminopropyltrimethoxysilane, and 0.5 part of stannous dihydroxylate into the planetary mixer, and keep the vacuum -0.08MPa, the stirring speed is 70rpm, stirring for 20 minutes to prepare component B. The product performance test results are shown in Table 1.
Embodiment 2
[0036] Put 100 parts of α, ω-dihydroxy polydimethylsiloxane with a viscosity of 1500 mPas at 25±2°C, and 300 parts of silicon micropowder, and knead them in a kneader at a temperature of 180°C and a vacuum of -0.08 MPa for 3 Hours, the base material is obtained after cooling. At room temperature, add 100 parts of base material, 50 parts of α, ω-dihydroxy polydimethylsiloxane, and 2 parts of high-hydroxyl silicone oil into the planetary mixer, keep the vacuum at -0.08MPa, and stir at a speed of 70rpm. 20 minutes to prepare component A; at room temperature, add 100 parts of ethyl silicate, 0.5 part of γ-aminoethylaminopropyltrimethoxysilane, and 0.3 part of stannous dihydroxylate into the planetary mixer, and keep the vacuum -0.08MPa, the stirring speed is 70rpm, stirring for 20 minutes to prepare component B. The product performance test results are shown in Table 1.
Embodiment 3
[0038] Put 100 parts of α, ω-dihydroxy polydimethylsiloxane with a viscosity of 1500 mPas at 25±2°C and 20 parts of fumed silica into a kneader at a temperature of 180°C and a vacuum of -0.08MPa After kneading for 3 hours, the base material was obtained after cooling. At room temperature, add 100 parts of base material, 50 parts of α, ω-dihydroxy polydimethylsiloxane, and 1 part of high-hydroxyl silicone oil into the planetary mixer, keep the vacuum at -0.08MPa, and stir at a speed of 70rpm. 20 minutes to prepare component A; at room temperature, add 100 parts of ethyl silicate, 0.5 part of γ-aminoethylaminopropyl trimethoxysilane, and 0.9 part of stannous dihydroxylate into the planetary mixer, and keep the vacuum -0.08MPa, the stirring speed is 70rpm, stirring for 20 minutes to prepare component B. The product performance test results are shown in Table 1.
PUM
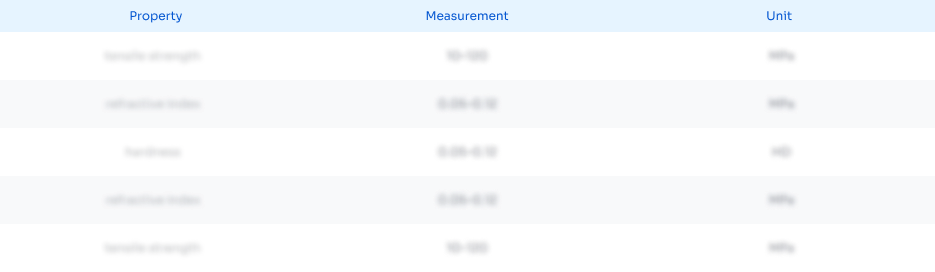
Abstract
Description
Claims
Application Information

- Generate Ideas
- Intellectual Property
- Life Sciences
- Materials
- Tech Scout
- Unparalleled Data Quality
- Higher Quality Content
- 60% Fewer Hallucinations
Browse by: Latest US Patents, China's latest patents, Technical Efficacy Thesaurus, Application Domain, Technology Topic, Popular Technical Reports.
© 2025 PatSnap. All rights reserved.Legal|Privacy policy|Modern Slavery Act Transparency Statement|Sitemap|About US| Contact US: help@patsnap.com