Disperse reactive dye one-bath two-step dip dyeing method for polyester cotton fabric
A technology of disperse activity and dyeing method, applied in the field of one-bath and two-step dip dyeing and dyeing of disperse reactive dyes, can solve the problems of no use value, affect the hand feeling of the fabric, uneven coloring, etc., and achieve excellent slow-release function and good leveling dyeing. effect of effect
- Summary
- Abstract
- Description
- Claims
- Application Information
AI Technical Summary
Problems solved by technology
Method used
Image
Examples
Embodiment 1
[0019] In the present embodiment, a kind of disperse reactive dye one-bath two-step exhaust dyeing method of polyester-cotton fabric comprises the following steps:
[0020] S1, pretreatment, according to the bath ratio of 1:5, pad the polyester-cotton fabric to be dyed with a finishing solution, the finishing solution includes: β-cyclodextrin 10g / L, 1,2,3,4-butane tetracarboxylic acid 5g / L, sodium hypophosphite 2g / L, two dipping and two rolling, the padding temperature is 30°C, the excess rate is 110%, pre-baking at 60°C for 6min, baking at 120°C for 5min, after washing in cold water, 50°C down drying;
[0021] S2, dyeing and washing, the polyester-cotton fabric after S1 treatment is immersed in the disperse dyeing solution, and described disperse dyeing solution comprises: disperse dye 5% (owf), glacial acetic acid 2g / L, sodium acetate 2g / L, Adjust the bath ratio to 1:5, enter the dyeing at 40°C, raise the temperature to 75°C at a rate of 2°C / min, hold for 5 minutes, then ra...
Embodiment 2
[0025] In the present embodiment, a kind of disperse reactive dye one-bath two-step exhaust dyeing method of polyester-cotton fabric comprises the following steps:
[0026] S1, pretreatment, according to the bath ratio 1:15, the polyester-cotton fabric to be dyed will be padded with the finishing liquid, and the finishing liquid includes: β-cyclodextrin 5g / L, citric acid 15g / L, sodium hypophosphite 0.5g / L L, two dipping and two rolling, the padding temperature is 40°C, the excess rolling rate is 80%, pre-bake at 80°C for 3 minutes, bake at 140°C for 1 minute, wash in cold water, and dry at 60°C;
[0027] S2, dyeing and washing, immerse the polyester-cotton fabric after S1 treatment in the disperse dyeing solution, and the disperse dyeing solution comprises: disperse dye 1% (owf), glacial acetic acid 4g / L, sodium acetate 1g / L, Adjust the bath ratio to 1:25, enter the dyeing at 30°C, raise the temperature to 65°C at a rate of 2.5°C / min, hold for 10 minutes, then raise the temper...
Embodiment 3
[0031] In the present embodiment, a kind of disperse reactive dye one-bath two-step exhaust dyeing method of polyester-cotton fabric comprises the following steps:
[0032] S1, pretreatment, according to bath ratio 1:10, padding finishing solution of polyester-cotton fabric to be dyed, described finishing solution comprises: β-cyclodextrin 7g / L, 1,2,3,4-butane tetracarboxylic acid 8g / L, sodium hypophosphite 1g / L, two dipping and two rolling, the padding temperature is 35°C, the excess rate is 95%, pre-baked at 70°C for 4 minutes, baked at 130°C for 3 minutes, washed in cold water, 55°C down drying;
[0033] S2, dyeing and washing, immersing the polyester-cotton fabric after S1 treatment in the disperse dye solution, the disperse dye solution comprising: disperse dye 3% (owf), glacial acetic acid 3g / L, sodium acetate 1.5g / L , adjust the bath ratio to 1:15, enter dyeing at 35°C, heat up to 70°C at a rate of 2.2°C / min, hold for 7 minutes, then raise the temperature to 120°C at a...
PUM
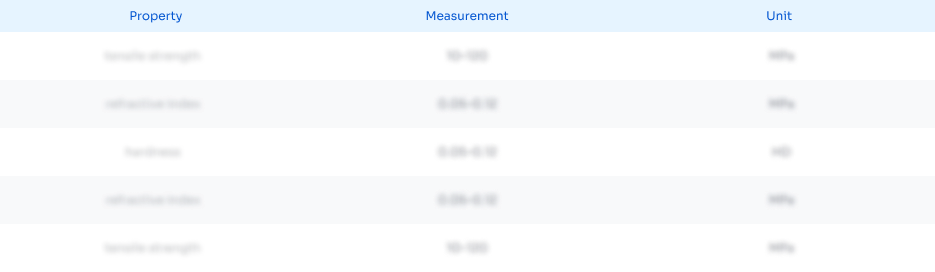
Abstract
Description
Claims
Application Information

- R&D
- Intellectual Property
- Life Sciences
- Materials
- Tech Scout
- Unparalleled Data Quality
- Higher Quality Content
- 60% Fewer Hallucinations
Browse by: Latest US Patents, China's latest patents, Technical Efficacy Thesaurus, Application Domain, Technology Topic, Popular Technical Reports.
© 2025 PatSnap. All rights reserved.Legal|Privacy policy|Modern Slavery Act Transparency Statement|Sitemap|About US| Contact US: help@patsnap.com