Smelting method capable of improving fluidity of molten steel after refining and desulfurizing of deformed steel bar
A smelting method and rebar technology, which is applied in the field of steel manufacturing, can solve problems such as poor fluidity of molten steel, and achieve the effect of ensuring normal pouring and improving fluidity of molten steel
- Summary
- Abstract
- Description
- Claims
- Application Information
AI Technical Summary
Problems solved by technology
Method used
Image
Examples
Embodiment 1
[0050] Converter smelting
[0051] ① Load 41 tons of scrap steel, 119 tons of molten iron, and a total load of 160 tons. The composition of molten iron into the furnace is Si: 0.31%, S: 0.056%, and temperature T: 1326°C; desulfurization process;
[0052] ② The top-bottom combined blowing mode is adopted, the amount of lime added: 5850kg, the tapping temperature: 1642°C, and the tapping amount is 149 tons.
[0053] (2) Post-furnace and argon station treatment
[0054] After the furnace alloying operation, the total time of bottom blowing is 4min, and the sampling of C: 0.204%, Si: 0.29%, Mn: 1.37%, P: 0.032%, S: 0.053%, V: 0.024%.
[0055] (3) LF refining
[0056] ① Add slagging material before refining and power transmission, lime addition is 690kg, 100kg fluorite is added, and 60kg carbon powder is added during power transmission for diffusion deoxidation;
[0057] ② Power on for 8 minutes, power off, blow argon at the bottom of the large ladle, stir for 2 minutes, take s...
Embodiment 2
[0064] (1) Converter smelting
[0065] ① Load 40 tons of scrap steel, 121 tons of molten iron, and a total load of 161 tons. The composition of molten iron into the furnace is Si: 0.28%, S: 0.067%, and temperature T: 1319°C; desulfurization process;
[0066] ② Adopt the top-bottom combined blowing mode, the amount of lime added: 5950kg, the tapping temperature: 1645 ℃, and the tapping amount is 150 tons.
[0067] (2) Post-furnace and argon station treatment
[0068] After the furnace alloying operation, the total time of bottom blowing is 5min, and the argon station samples C: 0.217%, Si: 0.29%, Mn: 1.39%, P: 0.035%, S: 0.062%, V: 0.023%.
[0069] (3) LF refining
[0070] ① Add slagging material before refining and power transmission, lime addition is 800kg, 150kg fluorite is added, and 60kg calcium carbide is added during power transmission for diffusion deoxidation;
[0071] ② Power on for 8 minutes, power off, blow argon at the bottom of the large ladle, stir for 2 minu...
Embodiment 3
[0078] Converter smelting
[0079] ① Charge 42 tons of scrap steel, 121 tons of molten iron, and a total load of 163 tons. The composition of the molten iron into the furnace is Si: 0.42%, S: 0.036%, and the temperature T: 1363°C; the scrap steel contains iron castings, and the molten steel in the furnace is sampled : 0.076%, it is determined that the refining desulfurization process will be adopted in the next step;
[0080] ② The top-bottom combined blowing mode is adopted, the amount of lime added: 5600kg, the tapping temperature: 1650°C, and the tapping amount is 150 tons.
[0081] (2) Post-furnace and argon station treatment
[0082] After the furnace alloying operation, the total time of bottom blowing is 4min, and the argon station samples C: 0.211%, Si: 0.30%, Mn: 1.36%, P: 0.037%, S: 0.075%, V: 0.023%.
[0083] (3) LF refining
[0084] ① Add slag-making material before refining and power transmission, the amount of lime added is 1100kg, 200kg of fluorite is added, ...
PUM
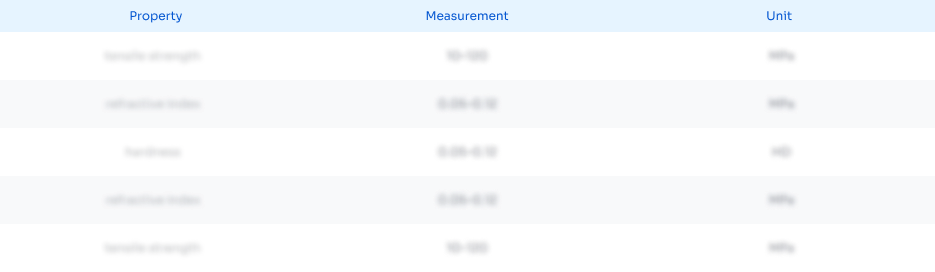
Abstract
Description
Claims
Application Information

- Generate Ideas
- Intellectual Property
- Life Sciences
- Materials
- Tech Scout
- Unparalleled Data Quality
- Higher Quality Content
- 60% Fewer Hallucinations
Browse by: Latest US Patents, China's latest patents, Technical Efficacy Thesaurus, Application Domain, Technology Topic, Popular Technical Reports.
© 2025 PatSnap. All rights reserved.Legal|Privacy policy|Modern Slavery Act Transparency Statement|Sitemap|About US| Contact US: help@patsnap.com