Polylactic acid plastic containing composite flame retardant and preparation method of polylactic acid plastic
A technology of polylactic acid and flame retardant, applied in the field of degradable plastics
- Summary
- Abstract
- Description
- Claims
- Application Information
AI Technical Summary
Problems solved by technology
Method used
Image
Examples
Embodiment 1
[0026] This embodiment provides a polylactic acid plastic containing a composite flame retardant, which is made of the following raw materials in parts by weight: 110 parts of polylactic acid, 15 parts of plant fiber, 2 parts of pentaerythritol, 1.5 parts of starch, and 12 parts of ammonium polyphosphate. part, 4 parts of melamine, 2 parts of modified white carbon black, 5 parts of ethylene oxide, 0.5 part of sorbitol, 1.5 parts of talcum powder, 1.5 parts of stearic acid amide, 10100.25 parts of antioxidant.
[0027] Wherein, the plant fiber is made through the following surface treatment:
[0028] (1) Take 3.5 g of sodium alginate, add it to 100 ml of water, stir to dissolve, and then adjust the pH value to 7 with acetic acid to obtain a sodium alginate solution.
[0029] (2) Take plant fibers and pulverize them, and then carry out air-explosion loosening treatment; add the plant fibers after air-explosion loosening treatment into sodium alginate solution and soak for 4 hour...
Embodiment 2
[0037] This embodiment provides a polylactic acid plastic containing a composite flame retardant, which is made of the following raw materials in parts by weight: 100 parts of polylactic acid, 20 parts of plant fiber, 1 part of pentaerythritol, 2 parts of starch, and 10 parts of ammonium polyphosphate 5 parts of melamine, 1 part of modified white carbon black, 6 parts of ethylene oxide, 0.2 part of sorbitol, 2 parts of talcum powder, 1 part of stearic acid amide, 0.4 part of antioxidant 1010.
[0038] Wherein, the plant fiber is made through the following surface treatment:
[0039] (1) Take 2 g of sodium alginate, add it to 100 ml of water, stir to dissolve, and then adjust the pH value to 9 with acetic acid to obtain a sodium alginate solution.
[0040] (2) Take the plant fiber and pulverize it, and then carry out air-explosion loosening treatment; add the plant fiber after the air-explosion loosening treatment into sodium alginate solution and soak for 5 hours, filter and d...
Embodiment 3
[0048]This embodiment provides a polylactic acid plastic containing a composite flame retardant, which is made of the following raw materials in parts by weight: 120 parts of polylactic acid, 10 parts of plant fiber, 3 parts of pentaerythritol, 1 part of starch, and 15 parts of ammonium polyphosphate 3 parts, 3 parts of melamine, 3 parts of modified white carbon black, 4 parts of ethylene oxide, 0.8 part of sorbitol, 1 part of talcum powder, 2 parts of stearic acid amide, 0.1 part of antioxidant 168.
[0049] Wherein, the plant fiber is made through the following surface treatment:
[0050] (1) Take 5 g of sodium alginate, add it to 100 ml of water, stir to dissolve, and then adjust the pH value to 5 with acetic acid to obtain a sodium alginate solution.
[0051] (2) Take plant fibers and pulverize them, and then carry out air-explosion loosening treatment; add the plant fibers after air-explosion loosening treatment into sodium alginate solution and soak for 3 hours, filter a...
PUM
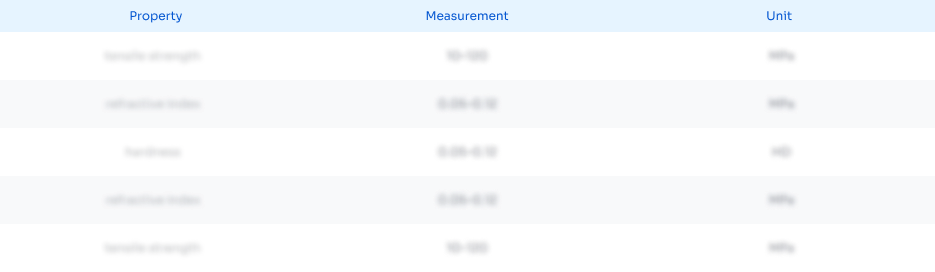
Abstract
Description
Claims
Application Information

- R&D Engineer
- R&D Manager
- IP Professional
- Industry Leading Data Capabilities
- Powerful AI technology
- Patent DNA Extraction
Browse by: Latest US Patents, China's latest patents, Technical Efficacy Thesaurus, Application Domain, Technology Topic, Popular Technical Reports.
© 2024 PatSnap. All rights reserved.Legal|Privacy policy|Modern Slavery Act Transparency Statement|Sitemap|About US| Contact US: help@patsnap.com