Process for producing trimellitic anhydride by continuous oxidizing process
A technology of trimellitic anhydride and oxidation process, which is applied in the field of producing trimellitic anhydride by adopting a continuous air liquid-phase oxidation process, can solve the problems of short service life of equipment, small production scale, unstable quality and the like, and achieves high production safety, high production efficiency, The effect of stable product quality
- Summary
- Abstract
- Description
- Claims
- Application Information
AI Technical Summary
Problems solved by technology
Method used
Image
Examples
Embodiment 1
[0034] Embodiment 1: Accurately measure 2000Kg of the partial trimethylbenzene raw material in the above technical scheme, accurately measure 8000Kg of acetic acid solvent, join in the batching kettle 4 with delivery pump, then add cobalt acetate, manganese acetate, tetrabromoethane or hydrogen bromide 6Kg each, stir evenly, keep the temperature at 80°C, pass the reaction feed pump at 2m 3 The flow rate of / h is added to the oxidation reactor 5. When the reactor shows 30% liquid level, stop adding, then feed compressed air to boost the pressure to 1.0Mpa, turn on the heat conduction oil and heat it to 150°C to initiate the reaction. When the reaction tail oxygen When the meter shows that the oxygen content in the vented tail gas moves up from zero, turn on the reaction feed pump, with a rate of 2m 3 The flow rate of / h is continuously fed into the reactor 5, and the feed rate of the compressed air is adjusted to control the oxygen content in the reaction exhaust tail gas at ab...
Embodiment 2
[0036] Embodiment 2: Accurately measure 3000Kg and 18000Kg of acetic acid solvent in the above-mentioned technical scheme, add in the batching kettle 4 with a delivery pump, then add cobalt acetate, manganese acetate, tetrabromoethane or hydrogen bromide 21Kg each, stir evenly, keep the temperature at 95°C, pass the reaction feed pump at 2m 3 The flow rate of / h is added to the oxidation reactor 5, and when the reactor shows 25% liquid level, stop adding, then feed compressed air to boost the pressure to 2.0Mpa, turn on the heat conduction oil and heat to 200°C to initiate the reaction, when the reaction tail oxygen When the meter shows that the oxygen content in the vented tail gas moves up from zero, turn on the reaction feed pump, with a rate of 2m 3 The flow rate of / h is continuously fed into the reactor 5, and the feed rate of the compressed air is adjusted to control the oxygen content in the reaction exhaust tail gas at about 6% (volume percentage), and make it reach a...
Embodiment 3
[0038] Embodiment 3: Accurately measure 5000Kg of the partial trimethylbenzene raw material in the above technical scheme, accurately measure 45000Kg of acetic acid solvent, join in the batching kettle 4 with delivery pump, then add cobalt acetate, manganese acetate, tetrabromoethane or hydrogen bromide 100Kg each, stir evenly, keep the temperature at 60°C, pass the reaction feed pump at 2m 3 The flow rate of / h is added to the oxidation reactor 5, stop adding when the reactor shows 20% liquid level, then feed compressed air to boost the pressure to 3.5Mpa, open the heat conduction oil and heat to 280°C to initiate the reaction, when the reaction tail oxygen When the meter shows that the oxygen content in the vented tail gas moves up from zero, turn on the reaction feed pump, with a rate of 2m 3 The flow rate of / h is continuously fed into the reactor 5, and the feed rate of the compressed air is adjusted to control the oxygen content in the reaction exhaust tail gas at about ...
PUM
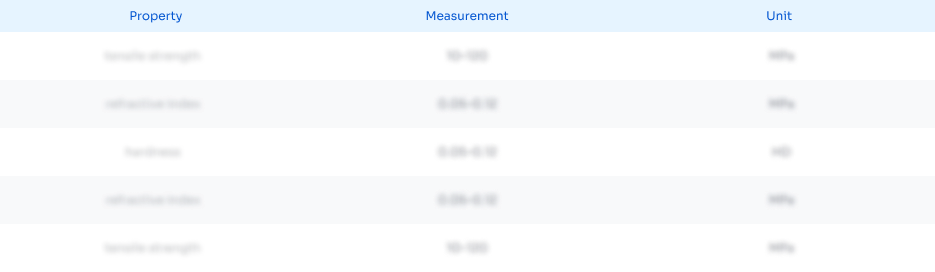
Abstract
Description
Claims
Application Information

- R&D
- Intellectual Property
- Life Sciences
- Materials
- Tech Scout
- Unparalleled Data Quality
- Higher Quality Content
- 60% Fewer Hallucinations
Browse by: Latest US Patents, China's latest patents, Technical Efficacy Thesaurus, Application Domain, Technology Topic, Popular Technical Reports.
© 2025 PatSnap. All rights reserved.Legal|Privacy policy|Modern Slavery Act Transparency Statement|Sitemap|About US| Contact US: help@patsnap.com