A Synergistic Emission Reduction Method for Energy-carrying Composite Gas Media Sintering
A composite gas and medium technology, applied in the field of sintering, iron and steel metallurgy sintering, to achieve the effect of reducing emissions, significant emission reduction effects, and reducing the generation of pollutants
- Summary
- Abstract
- Description
- Claims
- Application Information
AI Technical Summary
Problems solved by technology
Method used
Image
Examples
Embodiment 1
[0033] According to the mass ratio of 59.81% mixed iron ore, 4.42% dolomite, 5.38% limestone, 3.46% quicklime, 13.85% sintered ore return, 9.23% blast furnace return ore, and 3.85% coke powder (the chemical composition of the obtained sintered ore is TFe56. 26%, R1.80, MgO1.80%, CaO10.83%). The total area of the sintering machine is 450m 2 , a total of 24 bellows. After the raw materials are mixed and granulated, they are placed on the sintering trolley, and the hot exhaust gas of the ring cooler (temperature 250°C, O 2 content 20.90%) into the ignition cover of the ignition section (accounting for 2 / 24 of the length of the sintering machine) for hot blast ignition. Introduce hot waste gas (temperature 200°C, O 2 content of 20.90%) for heat preservation, and cascade spraying of natural gas in the heat preservation cover, the concentration along the length direction of the sintering machine is uniformly reduced from 0.60% to 0.3%. Inject 0.3% natural gas into the middle s...
Embodiment 2
[0035] According to the mass ratio of 59.81% mixed iron ore, 4.42% dolomite, 5.38% limestone, 3.46% quicklime, 13.85% sintered ore return, 9.23% blast furnace return ore, and 3.85% coke powder (the chemical composition of the obtained sintered ore is TFe56. 26%, R1.80, MgO1.80%, CaO10.83%). The total area of the sintering machine is 450m 2 , a total of 24 bellows. After the raw materials are mixed and granulated, they are placed on the sintering trolley, and the hot exhaust gas of the ring cooler and the hot exhaust gas of the blast furnace gas (temperature 350 ° C, O 2 content 20.0%) into the ignition cover of the ignition section (accounting for 1 / 24 of the length of the sintering machine) for hot blast ignition. Introduce hot waste gas (temperature 300°C, O 2 content 20.0%) for heat preservation, and cascade spraying of natural gas in the heat preservation cover, the concentration along the length direction of the sintering machine is uniformly reduced from 0.50% to 0....
Embodiment 3
[0037] According to the mass ratio of mixed iron ore 60.03%, dolomite 4.44%, limestone 5.37%, quicklime 3.46%, sinter return ore 13.85%, blast furnace return ore 9.23%, coke powder 3.62% batching (the chemical composition of the obtained sinter is TFe56. 29%, R1.80, MgO1.80%, CaO10.81%). The total area of the sintering machine is 450m 2 , a total of 24 bellows. After the raw materials are mixed and granulated, they are placed on the sintering trolley, and the hot exhaust gas of the ring cooler and the hot exhaust gas of the blast furnace gas are burned (temperature 300°C, O 2 content 20.40%) into the ignition cover of the ignition section (accounting for 2 / 24 of the length of the sintering machine) for hot blast ignition. Introduce hot waste gas (temperature 250°C, O 2 content 20.40%) for heat preservation, and cascade spraying of natural gas in the heat preservation cover, the concentration along the length direction of the sintering machine is uniformly reduced from 0.6...
PUM
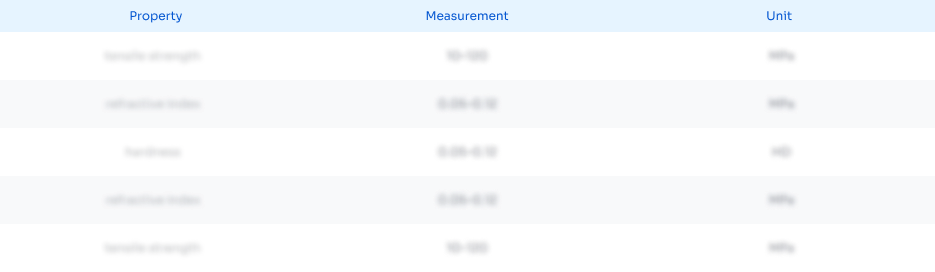
Abstract
Description
Claims
Application Information

- Generate Ideas
- Intellectual Property
- Life Sciences
- Materials
- Tech Scout
- Unparalleled Data Quality
- Higher Quality Content
- 60% Fewer Hallucinations
Browse by: Latest US Patents, China's latest patents, Technical Efficacy Thesaurus, Application Domain, Technology Topic, Popular Technical Reports.
© 2025 PatSnap. All rights reserved.Legal|Privacy policy|Modern Slavery Act Transparency Statement|Sitemap|About US| Contact US: help@patsnap.com