Preparation method of low-voltage self-repairing aluminum alloy micro-arc oxidation film
A micro-arc oxidation and self-healing technology, applied in anodizing, electrolytic coatings, surface reaction electrolytic coatings, etc., can solve problems such as affecting corrosion resistance and wear resistance, loss of electrical energy, etc., to improve product performance, reduce energy consumption, The simple effect of sewage treatment
- Summary
- Abstract
- Description
- Claims
- Application Information
AI Technical Summary
Problems solved by technology
Method used
Examples
Embodiment 1
[0024] 1. The sample is made of 2024 aluminum alloy plate, cut into a 25mm×20mm×2mm rectangle, and holes are punched on the edge of the sample for connecting wires;
[0025] 2. Use sandpaper to polish the surface of the sample to 1500#, put it into an ultrasonic cleaner, clean it with absolute ethanol, and dry it for later use;
[0026] 3. Electrolyte adopts silicate system, sodium silicate nonahydrate 15g L -1 , Potassium hydroxide 5g·L -1 ; Corrosion inhibitor nano serpentine particles 6g L -1 , dispersant polyethylene glycol 1g L -1 ; Additive potassium fluoride 10g L -1 , glycerin 1ml·L -1 ;
[0027] 4. Use a pulse power supply for micro-arc oxidation, adopt constant voltage mode, increase the voltage step by step, and finally increase to 200V, and the oxidation time is 10 minutes. After the reaction is completed, use deionized water and absolute ethanol to clean and dry.
Embodiment 2
[0029] 1. The sample is made of 2024 aluminum alloy plate, cut into a 25mm×20mm×2mm rectangle, and holes are punched on the edge of the sample for connecting wires;
[0030] 2. Use sandpaper to polish the surface of the sample to 1500#, put it into an ultrasonic cleaner, clean it with absolute ethanol, and dry it for later use;
[0031] 3. The electrolyte uses a silicate system, sodium silicate nonahydrate 5g L -1 , Potassium hydroxide 1g·L -1 ; Corrosion inhibitor nano serpentine particles 8g L -1 , dispersant polyethylene glycol 1g·L -1 ; Additive potassium fluoride 10g L -1 , glycerin 1ml·L -1 ;
[0032] 4. Use a pulse power supply for micro-arc oxidation, adopt constant voltage mode, increase the voltage step by step, and finally increase to 200V, and the oxidation time is 10 minutes. After the reaction is completed, use deionized water and absolute ethanol to clean and dry.
Embodiment 3
[0034] 1. The sample is made of 2024 aluminum alloy plate, cut into a 25mm×20mm×2mm rectangle, and holes are punched on the edge of the sample for connecting wires;
[0035] 2. Use sandpaper to polish the surface of the sample to 1500#, put it into an ultrasonic cleaner, clean it with absolute ethanol, and dry it for later use;
[0036] 3. Electrolyte adopts silicate system, sodium silicate nonahydrate 10g L -1 , Potassium hydroxide 1g·L -1 ; Corrosion inhibitor nano serpentine particles 10g L -1 , dispersant polyethylene glycol 1g L -1 ; Additive potassium fluoride 10g L -1 , glycerin 1ml·L -1 ;
[0037] 4. Use a pulse power supply for micro-arc oxidation, adopt constant voltage mode, increase the voltage step by step, and finally increase to 200V, and the oxidation time is 10 minutes. After the reaction is completed, use deionized water and absolute ethanol to clean and dry.
PUM
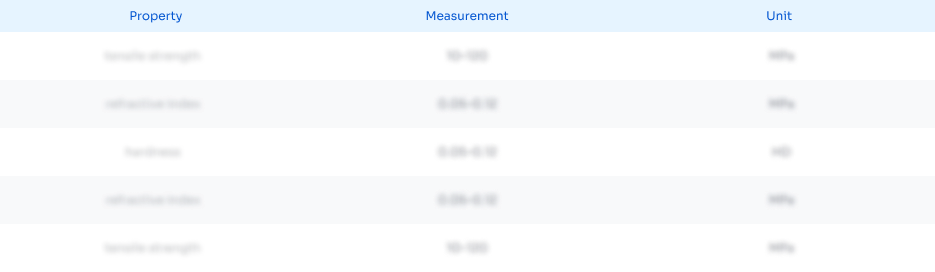
Abstract
Description
Claims
Application Information

- R&D Engineer
- R&D Manager
- IP Professional
- Industry Leading Data Capabilities
- Powerful AI technology
- Patent DNA Extraction
Browse by: Latest US Patents, China's latest patents, Technical Efficacy Thesaurus, Application Domain, Technology Topic, Popular Technical Reports.
© 2024 PatSnap. All rights reserved.Legal|Privacy policy|Modern Slavery Act Transparency Statement|Sitemap|About US| Contact US: help@patsnap.com