Method for duplex smelting for high-nitrogen steel through pressurized ladle refining and pressurized electroslag remelting
A technology of pressurized electroslag and ladle refining, applied in the field of pressurized ladle refining and pressurized electroslag remelting double smelting of high-nitrogen steel, which can solve the problems of disturbing the smelting process, high requirements for measurement and control systems, and easy silicon increase, etc. question
- Summary
- Abstract
- Description
- Claims
- Application Information
AI Technical Summary
Problems solved by technology
Method used
Image
Examples
preparation example Construction
[0107] The preparation method provided by the present invention adopts the combination of bottom blowing nitrogen and pressurized gas phase-liquid steel interface nitriding to carry out nitrogen alloying, which has high efficiency and uniform nitrogen distribution, and then carries out pressurized electroslag remelting to further remove molten steel The inclusions and impurity elements in the high-nitrogen steel make up for the insufficient removal of inclusions and impurity elements in the pressurized ladle refining process, and improve the hot workability of the steel, so that the internal structure of the high-nitrogen steel is uniform and dense. The preparation method is simple and suitable for use. in industrial mass production.
[0108] In the present invention, the molten steel produced by AOD+LF furnace, VOD+LF furnace or converter+LF furnace is used as raw material, and nitrogen is blown from the bottom in a pressurized ladle furnace and gas phase-liquid steel interfac...
Embodiment 1
[0118] The smelting equipment used is an 80t pressurized ladle refining furnace and a 20t pressurized electroslag remelting furnace. The maximum pressure is 5MPa, the inner diameter D of the crystallizer is 950mm, and the weight of the consumable electrode is about 15t.
[0119] Calculated by formula I, formula II, formula V and formula VI to get p 1 is 0.40MPa, bottom blowing pressure p 2 is 1.02MPa, casting pressure p 5 It is 1.10MPa, the pressurized electroslag remelting pressure p 6 is 1.50MPa. The smelting raw materials and their quality are as follows: AOD+LF furnace produces 80.11t of molten steel, 80.30kg of nickel-magnesium alloy (80Ni-20Mg) and 40.13kg of cerium.
[0120] The composition of molten steel is: C: 0.33%, Mn: 0.42%, Cr: 15.50%, Si: 0.52%, Mo: 1.03%, S: 0.015%, P: 0.008% and the balance of Fe.
[0121] The target composition of high nitrogen martensitic stainless steel 30Cr15Mo1N is: C: 0.32%, Mn: 0.40%, Cr: 15.30%, Si: 0.50%, Mo: 1.0%, N: 0.40%, S: ≤...
Embodiment 2
[0138] The smelting equipment used is an 80t pressurized ladle refining furnace and a 20t pressurized electroslag remelting furnace. The maximum pressure is 5MPa, the inner diameter D of the crystallizer is 950mm, and the weight of the consumable electrode is about 15t.
[0139] Calculated by formula I, formula II, formula V and formula VI to get p 1 0.10MPa, bottom blowing pressure p 2 is 0.70MPa, casting pressure p 5 is 0.80MPa, and the pressure of electroslag remelting is p 6 is 1.50MPa. The smelting raw materials and their quality are as follows: VOD+LF furnace produces 80.12t of molten steel, 80.20kg of nickel-magnesium alloy (80Ni-20Mg) and 40.10kg of cerium.
[0140] The composition of molten steel is: C: 0.55%, Mn: 0.42%, Cr: 17.41%, Si: 0.46%, Mo: 1.13%, S: 0.020%, P: 0.008% and the balance of Fe.
[0141] The target composition of high nitrogen martensitic stainless steel 55Cr18Mo1VN is C: 0.54%, Mn: 0.40%, Cr: 17.30%, Si: 0.45%, Mo: 1.10%, N: 0.20%, S: ≤0.01%, ...
PUM
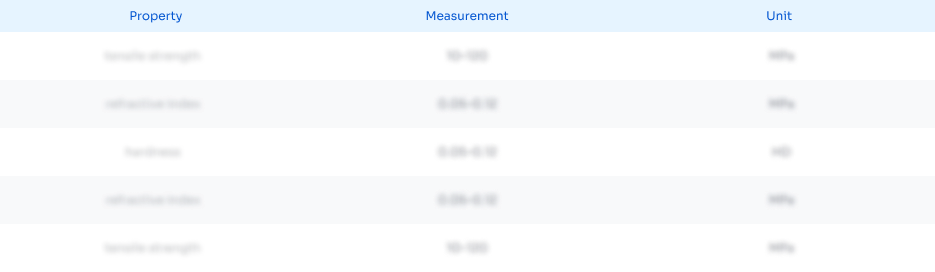
Abstract
Description
Claims
Application Information

- Generate Ideas
- Intellectual Property
- Life Sciences
- Materials
- Tech Scout
- Unparalleled Data Quality
- Higher Quality Content
- 60% Fewer Hallucinations
Browse by: Latest US Patents, China's latest patents, Technical Efficacy Thesaurus, Application Domain, Technology Topic, Popular Technical Reports.
© 2025 PatSnap. All rights reserved.Legal|Privacy policy|Modern Slavery Act Transparency Statement|Sitemap|About US| Contact US: help@patsnap.com