Method for preparing cyanuric acid by using ionic liquid
A technology of ionic liquid and cyanuric acid, applied in organic chemistry, bulk chemical production, etc., can solve the problems of not conforming to the concept of green chemistry, complex recycling process, expensive solvent, etc., to solve the problem of solvent evaporation and high heat transfer efficiency , the effect of reducing energy consumption
- Summary
- Abstract
- Description
- Claims
- Application Information
AI Technical Summary
Problems solved by technology
Method used
Image
Examples
Embodiment 1
[0026] Take an appropriate amount of 1-ethyl-3-methylimidazolium tetrafluoroborate ionic liquid, add it into the reaction kettle, start the stirring device, and start the vacuum circulation pump. When heating to 150°C, feed at a rate of 20Kg / min, and feed urea according to the ratio of solvent volume (mL) to urea mass (g) at 2:1. Rapidly heat to 210°C for condensation reaction. After reacting for 3 hours, the obtained slurry is cooled to room temperature and then centrifuged for 3 hours at a speed of 500 r / min. The centrifuged product is washed with distilled water and is crude cyanuric acid. Compared with the traditional direct pyrolysis method, the energy consumption is saved by 16%, the reaction yield is 89.4%, the purity of cyanuric acid is 90.7%, and the urea conversion rate is 81.1%.
Embodiment 2
[0028] Take an appropriate amount of 1-butyl-3-methylimidazolium tetrafluoroborate ionic liquid, add it into the reaction kettle, start the stirring device, and start the vacuum circulation pump. When heating to 140°C, feed at a rate of 30Kg / min, and the ratio of solvent volume (mL) to urea mass (g) is 2.5:1. Rapidly heat to 200°C for condensation reaction. After 4 hours of reaction, cool the resulting slurry to room temperature and centrifuge for 2.5 hours at a speed of 700r / min. The centrifuged product is washed with pure water, and the centrifuged product is crude cyanuric acid. Compared with the traditional direct pyrolysis method, the energy consumption is saved by 20%, the reaction yield is 87.3%, the purity of cyanuric acid is 93.5%, and the urea conversion rate is 81.6%.
Embodiment 3
[0030] Take an appropriate amount of 1-butyl-3-methylimidazolium dicyandiamide salt ionic liquid, add it to the reaction kettle, turn on the stirring device, turn on the vacuum circulation pump, and when heated to 145°C, feed at a constant speed of 20Kg / min. The ratio of solvent volume (mL) to urea mass (g) is 4:1. Rapidly heat to 190°C for condensation reaction. After reacting for 5 hours, the resulting slurry is cooled to room temperature and then centrifuged for 2 hours at a speed of 1000r / min. The centrifuged product is washed with distilled water, and the centrifuged product is crude cyanuric acid. Compared with the traditional direct pyrolysis method, energy consumption is saved by 24%, the reaction yield is 90.7%, the purity of cyanuric acid is 96.4%, and the conversion rate of urea is 87.4%.
PUM
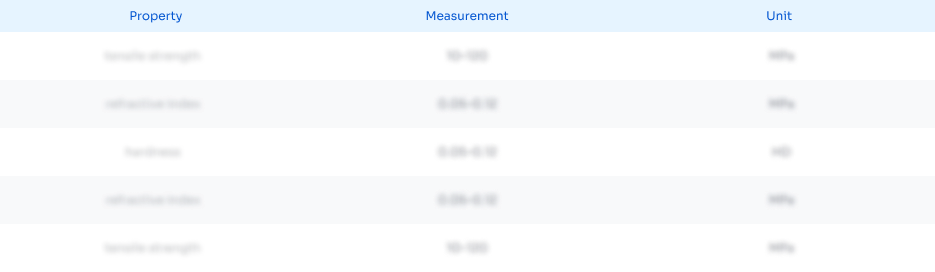
Abstract
Description
Claims
Application Information

- R&D Engineer
- R&D Manager
- IP Professional
- Industry Leading Data Capabilities
- Powerful AI technology
- Patent DNA Extraction
Browse by: Latest US Patents, China's latest patents, Technical Efficacy Thesaurus, Application Domain, Technology Topic, Popular Technical Reports.
© 2024 PatSnap. All rights reserved.Legal|Privacy policy|Modern Slavery Act Transparency Statement|Sitemap|About US| Contact US: help@patsnap.com