Converter less-slag smelting method
A low-slag smelting and converter technology, which is applied in the field of steelmaking, can solve the problems of prolonging the blowing time, increasing the cost, and failure to reach it, and achieve the effects of increasing the intensity of support, reducing the time of slag melting, and reducing the cost of power
- Summary
- Abstract
- Description
- Claims
- Application Information
AI Technical Summary
Problems solved by technology
Method used
Examples
Embodiment Construction
[0034] The technical solution of the present application will be further described below.
[0035] The slag-less smelting method of the converter adopts the low-slag-single-slag mode uniformly in the case of high iron consumption or low iron consumption, and complex changes in molten iron silicon. - Mixing molten iron - calculation - blowing - end point control - tapping;
[0036] (1) Retaining slag: keep the slag in the furnace after tapping the last furnace, and the amount of slag remaining is 50-80kg / t;
[0037] (2) Slag adjustment and slag splashing: turn on the nitrogen gas, adjust the gun position to the basic gun position, keep it for 25-30s, then raise the gun position to more than 2m, gradually press the gun according to the splashing of slag, and splash for 3 minutes At the same time, it is planned to add light-burned dolomite and lime to the bottom of the furnace, the amount added accounts for 2 / 3 of the total amount, and the furnace is shaken to a horizontal level...
PUM
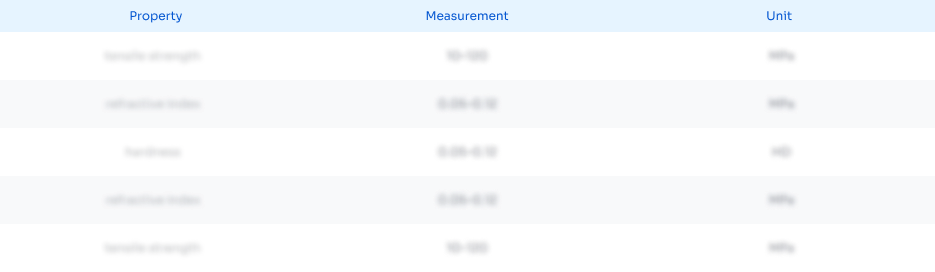
Abstract
Description
Claims
Application Information

- R&D
- Intellectual Property
- Life Sciences
- Materials
- Tech Scout
- Unparalleled Data Quality
- Higher Quality Content
- 60% Fewer Hallucinations
Browse by: Latest US Patents, China's latest patents, Technical Efficacy Thesaurus, Application Domain, Technology Topic, Popular Technical Reports.
© 2025 PatSnap. All rights reserved.Legal|Privacy policy|Modern Slavery Act Transparency Statement|Sitemap|About US| Contact US: help@patsnap.com