Breakpoint continuous printing method of surface exposure 3D printing equipment
A technology of 3D printing and surface exposure, applied in the field of 3D printing, can solve problems such as increasing equipment costs, achieve the effect of saving material costs, simple implementation methods, and avoiding the drop in accuracy of continuous printing at breakpoints
- Summary
- Abstract
- Description
- Claims
- Application Information
AI Technical Summary
Problems solved by technology
Method used
Image
Examples
Embodiment Construction
[0027] The present invention will be further described below in conjunction with the accompanying drawings and embodiments.
[0028] The present invention is described for the bottom-illuminated surface exposure equipment. The light source of the equipment is placed in the lower part of the equipment, and the bottom of the resin tank is irradiated upward from the bottom of the resin tank. The Z-axis drives the forming plate to move upward for layer-by-layer curing. For top-illuminated equipment, it is only necessary to change the direction of Z-axis movement and the position of the upper and lower limit switches. The surface exposure equipment is composed of two parts, the upper computer and the lower computer. In the present invention, the upper computer is a mobile device with a Bluetooth communication module, which is responsible for controlling the light source to display sliced images, sending motion commands to control the movement of the lower computer, and obtaining i...
PUM
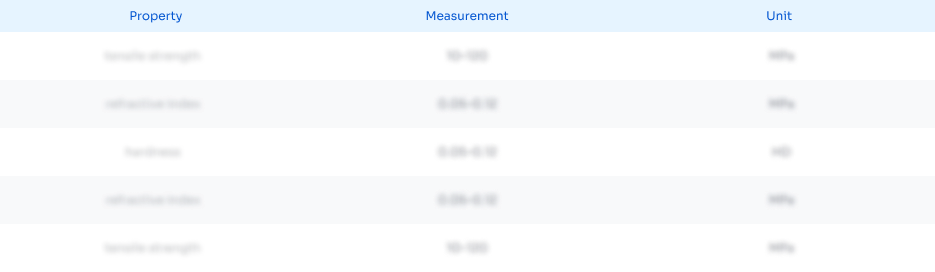
Abstract
Description
Claims
Application Information

- R&D Engineer
- R&D Manager
- IP Professional
- Industry Leading Data Capabilities
- Powerful AI technology
- Patent DNA Extraction
Browse by: Latest US Patents, China's latest patents, Technical Efficacy Thesaurus, Application Domain, Technology Topic, Popular Technical Reports.
© 2024 PatSnap. All rights reserved.Legal|Privacy policy|Modern Slavery Act Transparency Statement|Sitemap|About US| Contact US: help@patsnap.com