Preparation method of sprayed surface layer of environment-friendly polyurethane plastic track
A plastic runway and polyurethane technology, applied in polyurea/polyurethane coatings, coatings, roads, etc., can solve the problem that the comprehensive physical properties of the runway cannot fully meet the requirements of national standards, the polyurethane plastic runway is easy to foam, and the service life of the plastic runway is short, etc. problems, achieve the effect of eliminating the environmental threat of heavy metals, excellent curing effect, and low residual monomer content
- Summary
- Abstract
- Description
- Claims
- Application Information
AI Technical Summary
Problems solved by technology
Method used
Image
Examples
Embodiment 1
[0030] The raw material of the sprayed surface layer of an environment-friendly polyurethane plastic runway consists of component A, component B and an inert amine drier component. The proportioning ratio of raw materials of the present embodiment is as shown in table 1:
[0031] Table 1
[0032]
[0033] Drier component: N,N-dimethylcyclohexylamine, accounting for 0.5% of the mass of component B.
[0034] Preparation method of component A: Add the mixed polyether polyol N210 and N220 components into the reactor according to the formula, stir and heat up to 120°C, vacuum dehydrate until the mass fraction of water is 0.05%, cool down to 50°C, add TDI, Slowly raise the temperature to 60°C, stir at a constant temperature of 500r / min for 10 minutes, then continue to raise the temperature to 80°C, keep the constant temperature for 2 hours, cool down to 40°C, seal the storage tank, and set aside.
[0035] Preparation method of component B: put the above materials into the mixin...
Embodiment 2
[0038] The raw material of the sprayed surface layer of an environment-friendly polyurethane plastic runway consists of component A, component B and an inert amine drier component. The proportioning ratio of raw materials of the present embodiment is as shown in Table 2:
[0039] Table 2
[0040]
[0041] Drier component: N,N-dimethylcyclohexylamine, accounting for 0.3% of the mass of component B.
[0042] Preparation method of component A: Add the mixed polyether polyol MDI, N210, and N220 components into the reaction kettle according to the formula, stir and heat up to 130°C, vacuum dehydrate until the mass fraction of water is 0.04%, cool down to 50°C, add TDI, slowly raise the temperature to 60°C, stir at a constant temperature of 550r / min for 12 minutes, then continue to raise the temperature to 82°C, keep the constant temperature for 2.5 hours, cool down to 40°C, seal the storage tank, and set aside.
[0043] Preparation method of component B: put the above material...
Embodiment 3
[0046] The raw material of the sprayed surface layer of an environment-friendly polyurethane plastic runway consists of component A, component B and an inert amine drier component. The proportioning ratio of raw materials of the present embodiment is as shown in table 3:
[0047] table 3
[0048]
[0049] Drier component: N,N-dimethylcyclohexylamine, accounting for 0.5% of the mass of component B.
[0050]Preparation method of component A: Add the mixed polyether polyol N220 and N320 components into the reactor according to the formula, stir and heat up to 110°C, vacuum dehydrate until the mass fraction of water is 0.04%, cool down to 50°C, add TDI, Slowly raise the temperature to 60°C, stir at a constant temperature of 600r / min for 10 minutes, then continue to raise the temperature to 80°C, keep the constant temperature for 2 hours, cool down to 40°C and seal the storage tank for later use.
[0051] Preparation method of component B: put the above materials into the mixi...
PUM
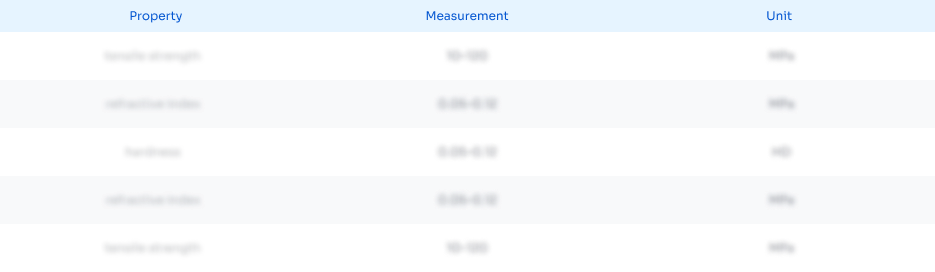
Abstract
Description
Claims
Application Information

- R&D
- Intellectual Property
- Life Sciences
- Materials
- Tech Scout
- Unparalleled Data Quality
- Higher Quality Content
- 60% Fewer Hallucinations
Browse by: Latest US Patents, China's latest patents, Technical Efficacy Thesaurus, Application Domain, Technology Topic, Popular Technical Reports.
© 2025 PatSnap. All rights reserved.Legal|Privacy policy|Modern Slavery Act Transparency Statement|Sitemap|About US| Contact US: help@patsnap.com