Method for preparing calcium aluminate by synergistic treatment of high-magnesium aluminum ash and fly ash
A high-magnesium aluminum ash and synergistic processing technology, which is applied in the preparation of calcium aluminate, alkaline earth metal aluminate/alumina/aluminum hydroxide, and aluminum silicate, can solve the problems of low synthesis temperature, high raw material cost, and production cost. Low-level problems, to achieve the effect of high reactivity and high decomposition rate
- Summary
- Abstract
- Description
- Claims
- Application Information
AI Technical Summary
Problems solved by technology
Method used
Image
Examples
Embodiment 1
[0029] Using aluminum ash (65.3% aluminum content, 6.0% magnesium oxide content) and high-alumina fly ash (32.0% aluminum content) from a recycled aluminum plant as raw materials, the high-magnesium aluminum ash slag, fly ash, and quicklime were mixed to control The molar ratio of Al:Ca is 1:1.20, and the molar ratio of Mg:Si is 1:1.15; the mixed material is subjected to wet ball milling, the liquid-solid ratio of the ball milling is 1:1, the pH of the ball milling is adjusted to 12 by NaOH, and the ball milling speed is 30r / min, The ball milling time is 3 hours; after the ball milling activation is completed, the material is washed and solid-liquid separated, and finally the mixed material is placed in an air atmosphere for high-temperature roasting, the roasting temperature is 1320 ° C, and the roasting time is 180 min. The roasted product can be used for steelmaking desulfurization calcium aluminate products. After testing, the relative content of calcium aluminate in the p...
Embodiment 2
[0031] Using aluminum ash (65.3% aluminum content, 6.0% magnesium oxide content) and high-alumina fly ash (32.0% aluminum content) from a recycled aluminum plant as raw materials, the high-magnesium aluminum ash slag, fly ash, and quicklime were mixed to control The molar ratio of Al:Ca is 1:1.32, and the molar ratio of Mg:Si is 1:1.05; the mixed material is subjected to wet ball milling, the liquid-solid ratio of the ball milling is 2:1, the pH of the ball milling is adjusted to 12 by NaOH, and the ball milling speed is 50r / min ball milling The time is 5 hours; after the ball mill activation is completed, the material is washed and separated from solid and liquid, and finally the mixed material is placed in an air atmosphere for high-temperature roasting, the roasting temperature is 1380 ° C, and the roasting time is 120 min. The roasted product can be used for steelmaking desulfurization Calcium aluminate products. After testing, the relative content of calcium aluminate in ...
Embodiment 3
[0033] Using aluminum ash (70.3% aluminum content, 12.0% magnesium oxide content) and high-aluminum fly ash (45.3% aluminum content) from a secondary aluminum plant as raw materials, the high-magnesium aluminum ash slag, fly ash, and quicklime were mixed to control The molar ratio of Al:Ca is 1:1.25, and the molar ratio of Mg:Si is 1:1.10; the mixed material is subjected to wet ball milling, the liquid-solid ratio of the ball milling is 3:1, the pH of the ball milling is adjusted to 13 by NaOH, and the milling speed is 20r / min, The ball milling time is 4 hours; after the ball milling activation is completed, the material is washed and solid-liquid separated, and finally the mixed material is placed in an air atmosphere for high-temperature roasting, the roasting temperature is 1350 ° C, and the roasting time is 155 min. The roasted product can be used for steelmaking desulfurization calcium aluminate products. After testing, the relative content of calcium aluminate in the pro...
PUM
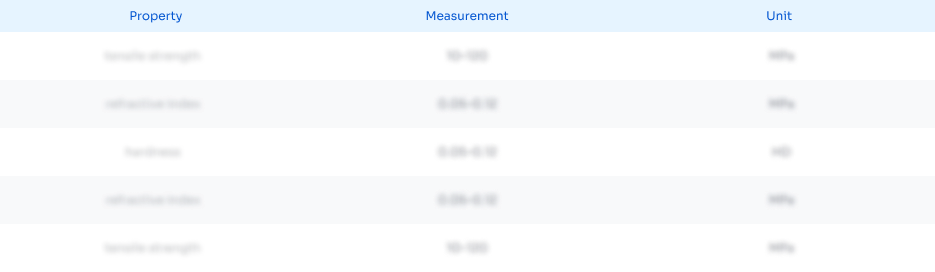
Abstract
Description
Claims
Application Information

- R&D
- Intellectual Property
- Life Sciences
- Materials
- Tech Scout
- Unparalleled Data Quality
- Higher Quality Content
- 60% Fewer Hallucinations
Browse by: Latest US Patents, China's latest patents, Technical Efficacy Thesaurus, Application Domain, Technology Topic, Popular Technical Reports.
© 2025 PatSnap. All rights reserved.Legal|Privacy policy|Modern Slavery Act Transparency Statement|Sitemap|About US| Contact US: help@patsnap.com