Preparation device for modified physical-property-reconstructed steel slag micro powder and application method
A steel slag fine powder and preparation device technology, which is applied in the field of comprehensive recycling of metallurgical slag resources, can solve the problems of waste of heat energy and low utilization rate of sensible heat of steel slag, and achieve the effects of reducing costs, eliminating land occupation by waste slag, and thinning the thickness of slag layer
- Summary
- Abstract
- Description
- Claims
- Application Information
AI Technical Summary
Problems solved by technology
Method used
Image
Examples
preparation example Construction
[0035] The method for preparing modified physical property reconstituted steel slag micropowder according to the present invention comprises the following steps:
[0036](1) Mix steel slag, reducing agent, additives and binders to make a mixture, add the mixture to the centrifugal field carbonization furnace through the packing chamber, and adopt the centrifugal field enhanced carbothermal reduction method to make the high-valent weak magnetic iron in the steel slag Fe2O3 is transformed into low-valence iron FeO and Fe3O4 and iron elemental Fe, and high-valence phosphorus P2O5 is transformed into elemental phosphorus P to obtain high-temperature preliminary modified physical properties of reconstituted steel slag;
[0037] (2) Put the high-temperature preliminary modified physical property restructured steel slag into the waste heat recovery system for waste heat recovery and utilization, remove the elemental phosphorus therein, and obtain the modified physical property restruc...
Embodiment 1
[0052] Put steel slag, coal gangue, calcium carbonate and bentonite into steel slag: coal gangue: calcium carbonate: bentonite = 100:33:15:5 according to the mass ratio, and put them into the carbonization furnace in the centrifugal field, and use the centrifugal field to strengthen the carbothermal reduction method for reduction roasting. The calcination temperature is 1300°C, and the calcination time is 30 minutes to obtain the dephosphorization reduction product. During the cooling process of the reduction product, the waste heat is recovered, and then the two-stage technology of vertical mill plus ultra-fine ball mill is used for grinding and high-current high-magnetism with a magnetic field strength of 1000mT. Technology for high-efficiency separation. After magnetic separation, the blown amount of steel slag fine powder is 10kg / tFe. Steel slag fine powder and fine coal powder are mixed according to the mass ratio of steel slag fine powder: fine coal powder = 0.8:1, and bla...
Embodiment 2
[0054] Put steel slag, coal gangue, calcium carbonate and bentonite into steel slag: coal gangue: calcium carbonate: bentonite = 100:33:15:5 according to the mass ratio, and put them into the carbonization furnace in the centrifugal field, and use the centrifugal field to strengthen the carbothermal reduction method for reduction roasting. The calcination temperature is 1400°C, and the calcination time is 20 minutes to obtain the dephosphorization reduction product. During the cooling process of the reduction product, the waste heat is recovered, and then the two-stage technology of vertical mill plus ultra-fine ball mill is used for grinding and high-current high-magnetism with a magnetic field strength of 1200mT. Technology for high-efficiency separation. After magnetic separation, the blown amount of steel slag fine powder is 15kg / tFe. Steel slag fine powder and fine coal powder are mixed according to the mass ratio of steel slag fine powder: fine coal powder = 1:1, and blast...
PUM
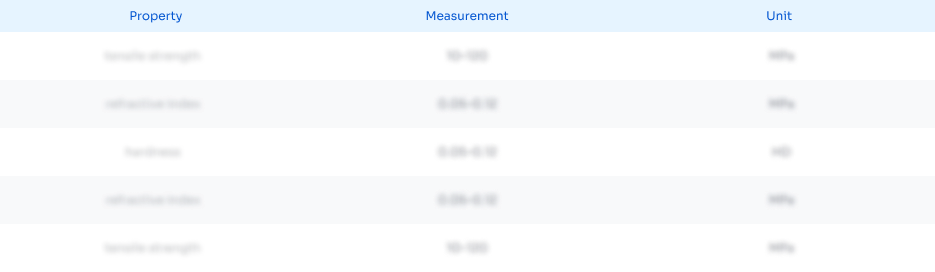
Abstract
Description
Claims
Application Information

- Generate Ideas
- Intellectual Property
- Life Sciences
- Materials
- Tech Scout
- Unparalleled Data Quality
- Higher Quality Content
- 60% Fewer Hallucinations
Browse by: Latest US Patents, China's latest patents, Technical Efficacy Thesaurus, Application Domain, Technology Topic, Popular Technical Reports.
© 2025 PatSnap. All rights reserved.Legal|Privacy policy|Modern Slavery Act Transparency Statement|Sitemap|About US| Contact US: help@patsnap.com