Environment-friendly interior wall coating and preparation method thereof
An interior wall coating, an environmentally friendly technology, applied in the direction of fireproof coatings, alkali metal silicate coatings, coatings, etc., can solve the problems of poor environmental protection, deterioration of the environment, and increased formaldehyde content
- Summary
- Abstract
- Description
- Claims
- Application Information
AI Technical Summary
Problems solved by technology
Method used
Image
Examples
preparation example 1
[0042] The preparation method of modified bentonite is: 1) disperse 10kg bentonite in 80kg mass fraction of 10% sulfuric acid solution, stir at 80°C for 4h to obtain bentonite suspension; 2) filter the suspension obtained in step 1), and use Wash the filtered filter cake with distilled water twice. After the washing, dry the filter cake, and then grind the dried filter cake to 100 mesh to obtain bentonite after acidification; 3) 5 kg of ferric nitrate is dissolved in 100 kg of In the water ethanol, ferric nitrate solution is obtained, then 50kg tetrabutyl titanate is added to the ferric nitrate solution, and 2kg parts of nitric acid solution with a mass fraction of 60wt% are added, and the mixed solution is obtained by stirring evenly; 4) the obtained in step 3) Add the mixed solution dropwise to 200kg of water, stir for 30min, and then let stand for 12h; 5) after standing, continue to add 25kg of the acidified bentonite in step 2) to step 4), stir for 2h, and let stand for 20h...
preparation example 2
[0044] The preparation method of modified bentonite is: 1) disperse 10kg bentonite in 90kg mass fraction of 30% sulfuric acid solution, stir at 90°C for 6h to obtain bentonite suspension; 2) filter the suspension obtained in step 1), and use Distilled water washes the filtered filter cake 4 times. After washing, dry the filter cake, and then grind the dried filter cake to 200 orders to obtain bentonite after acidification; 3) 5 kg of ferric nitrate is dissolved in 120 kg of In the water ethanol, ferric nitrate solution was obtained, then 60kg tetrabutyl titanate was added to the ferric nitrate solution, and 5kg mass fraction was added nitric acid solution of 68wt%, and the mixed solution was obtained by stirring; 4) the mixed solution obtained in step 3) Add dropwise to 250kg of water in the solution, after stirring for 60min, let it stand for 18h; 5) after standing, continue to add 35kg of the acidified bentonite in step 2) to step 4), stir for 3h, and let stand for 30h; 6 ) ...
preparation example 3
[0046] The preparation method of modified bentonite is: 1) disperse 10kg bentonite in 100kg mass fraction of 20% sulfuric acid solution, stir at 100°C for 5h to obtain bentonite suspension; 2) filter the suspension obtained in step 1), and use Wash the filtered filter cake with distilled water for 5 times. After washing, dry the filter cake, and then grind the dried filter cake to 150 mesh to obtain acidified bentonite; 3) 5 kg of ferric nitrate is dissolved in 110 kg of In water ethanol, ferric nitrate solution was obtained, then 55kg tetrabutyl titanate was added to the ferric nitrate solution, and 3.5kg parts of nitric acid solution with a mass fraction of 68wt% were added, and the mixed solution was obtained by stirring evenly; 4) Step 3) was obtained Add dropwise in 300kg of water in the mixed solution, after stirring for 45min, stand still for 24h; 5) After standing still, continue to add 30kg of bentonite after acidification in step 2) to step 4), after stirring for 3h, ...
PUM
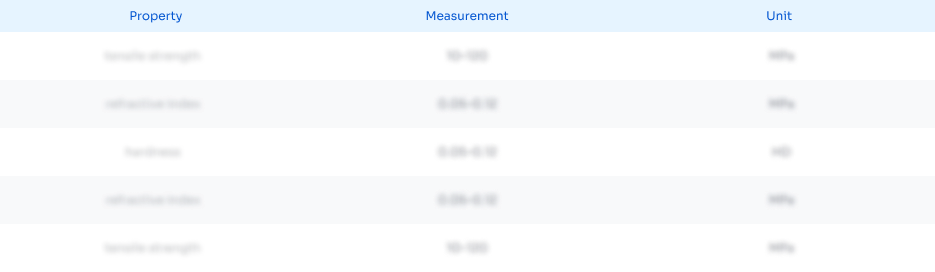
Abstract
Description
Claims
Application Information

- R&D
- Intellectual Property
- Life Sciences
- Materials
- Tech Scout
- Unparalleled Data Quality
- Higher Quality Content
- 60% Fewer Hallucinations
Browse by: Latest US Patents, China's latest patents, Technical Efficacy Thesaurus, Application Domain, Technology Topic, Popular Technical Reports.
© 2025 PatSnap. All rights reserved.Legal|Privacy policy|Modern Slavery Act Transparency Statement|Sitemap|About US| Contact US: help@patsnap.com