Magnesium or magnesium alloy surface hot-dip tinning or tin base alloy method
A technology of tin-based alloy and magnesium alloy, applied in the field of magnesium or magnesium alloy surface treatment, can solve problems such as short immersion plating time, and achieve the effects of good electrical conductivity, simple equipment and strong paintability
- Summary
- Abstract
- Description
- Claims
- Application Information
AI Technical Summary
Problems solved by technology
Method used
Image
Examples
example 1
[0031] Proceed as follows:
[0032] a. Pre-treat the AZ91D magnesium alloy workpiece (30×20×3mm), including alkali cleaning and pickling;
[0033] b. Activation treatment, place the workpiece in the activation solution for 8 minutes;
[0034] c. For pre-nickeling of magnesium alloy, place the above-mentioned activated sample in an alkaline nickel solution for 15 minutes, and the temperature of the plating solution is 78-82°C;
[0035] D, help plating, the sample after nickel plating is dipped in help plating solution (the hydrochloric acid 100ml / L of zinc chloride 700g / L and mass fraction 38%) in help plating 2 minutes;
[0036] e, drying, drying the workpiece after plating at 250°C for 5 minutes;
[0037] f. Hot-dip, heating and melting the tin alloy, hot-dip plating at 290-310°C, hot-dip the workpiece for 10 seconds, and take it out;
[0038] g. Thermal diffusion, heat treatment the workpiece at 220° for 60 minutes to increase the bonding force of the coating and obtain b...
example 2
[0041] Proceed as follows:
[0042] a. Pretreatment of AZ31 magnesium alloy workpiece (30×20×3mm), including alkali cleaning and pickling;
[0043] b. Activation treatment, place the workpiece in the activation solution for 8 minutes;
[0044] c, nickel plating, the above-mentioned activated sample is placed in alkaline nickel solution and plated for 15 minutes;
[0045] D, help plating, the sample after nickel plating is dipped in help plating solution (zinc chloride 700g / L and ammonium hydrogen chloride 36g / L) in help plating 2 minutes;
[0046] e, drying, drying the workpiece after plating at 250°C for 5 minutes;
[0047] f. Hot-dip, heat and melt the tin, perform hot-dip plating at 330-350°C, perform hot-dip plating on the workpiece for 20 seconds, and take it out;
[0048] g. Thermal diffusion, heat treatment the workpiece at 220° for 60 minutes to increase the bonding force of the coating and obtain better surface quality.
[0049] Examples show that a bright and smo...
example 3
[0051] Proceed as follows:
[0052] a. Pretreatment of pure magnesium workpiece (20×20×10mm), including alkali cleaning and pickling;
[0053] b. Activation treatment, place the workpiece in the activation solution for 8 minutes;
[0054] c, nickel plating, the above-mentioned activated sample is placed in alkaline nickel solution and plated for 15 minutes;
[0055] D, help plating, the sample after nickel plating is dipped in help plating solution (zinc chloride 700g / L and ammonium hydrogen chloride 36g / L) in help plating 2 minutes;
[0056] e, drying, drying the workpiece after plating at 250°C for 5 minutes;
[0057] f. Hot-dip, heating and melting the tin, hot-dip plating at 330-350°C, hot-dip the workpiece for 20 seconds, and take it out;
[0058] g. Thermal diffusion, heat treatment the workpiece at 220° for 90 minutes to increase the bonding force of the coating and obtain better surface quality.
[0059]Examples show that a bright and smooth tin layer is obtained o...
PUM
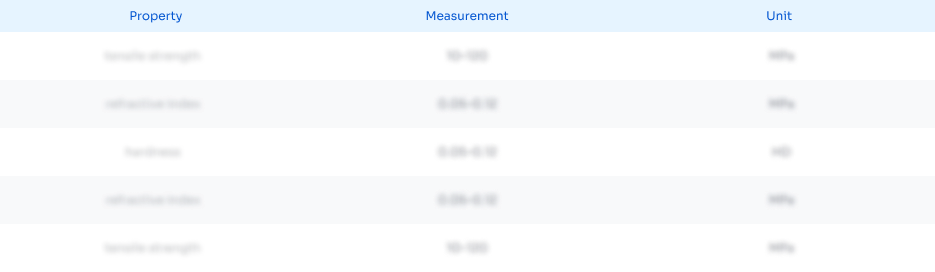
Abstract
Description
Claims
Application Information

- R&D
- Intellectual Property
- Life Sciences
- Materials
- Tech Scout
- Unparalleled Data Quality
- Higher Quality Content
- 60% Fewer Hallucinations
Browse by: Latest US Patents, China's latest patents, Technical Efficacy Thesaurus, Application Domain, Technology Topic, Popular Technical Reports.
© 2025 PatSnap. All rights reserved.Legal|Privacy policy|Modern Slavery Act Transparency Statement|Sitemap|About US| Contact US: help@patsnap.com