Mineral particle preparation method
A technology of microparticles and methods, applied in botany equipment and methods, chemicals for biological control, biocides, etc., can solve the problems of water consumption, harm to human body, environmental protection and other problems in the process, and achieve low production cost, The effect of streamlining production steps
- Summary
- Abstract
- Description
- Claims
- Application Information
AI Technical Summary
Problems solved by technology
Method used
Image
Examples
Embodiment 1
[0031] refer to Figures 1 to 4 , Example 1 of the mineral particle production method of the present invention includes a polyethylene glycol titanium preparation step S1, a mixing step S2, and a heating step S3.
[0032] In the step S1 of preparing titanium polyethylene glycol, first weigh 1000 grams (10 parts by weight) of ethylene glycol into the reaction bottle, and then slowly add 100 grams (1 part by weight) of titanium isopropoxide In ethylene glycol, and at room temperature, stirring at 200 rpm for 30 minutes, so that ethylene glycol and titanium isopropoxide are mixed and reacted to form a polyethylene glycol titanium solution. The polyethylene glycol titanium solution contains polyethylene glycol titanium and a small amount of unreacted titanium isopropoxide and ethylene glycol.
[0033] In the mixing step S2, first weigh 200g (2 parts by weight) of an aqueous acetic acid solution (containing 1 gram - 0.01 parts by weight of acetic acid) with a concentration of 0.5 ...
Embodiment 2
[0046] Embodiments 2 to 8 are similar to the embodiment 1, the difference is that in the heating step S3 in the embodiment 2, the temperature of the second mixed solution is maintained at about 90° C. In step S2, 10g (0.1 parts by weight) of silver nitrate solution is added. In the step of preparing titanium polyethylene glycol, 2500g (25 parts by weight) of ethylene glycol is used in Example 4. In Example 5, Similar to Example 4, but in the mixing step S2, further take more acetic acid aqueous solution (800g-that is, 8 parts by weight), embodiment 6 is similar to Example 5, but in the mixing step S2 Be to take more silver nitrate solution (200g-i.e. 2 parts by weight) further, the usage amount of the aqueous acetic acid solution of embodiment 7 is less, just be to only use 50g (0.5 parts by weight) in the mixing step S2 Acetic acid aqueous solution, the usage amount of the silver nitrate solution of embodiment 8 is more, just be to take the silver nitrate solution of 500g (5 ...
PUM
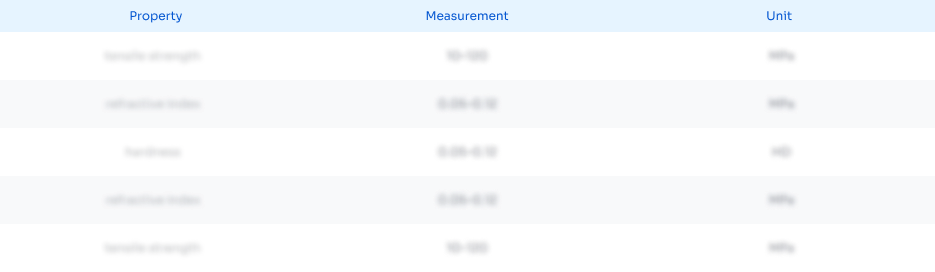
Abstract
Description
Claims
Application Information

- R&D Engineer
- R&D Manager
- IP Professional
- Industry Leading Data Capabilities
- Powerful AI technology
- Patent DNA Extraction
Browse by: Latest US Patents, China's latest patents, Technical Efficacy Thesaurus, Application Domain, Technology Topic, Popular Technical Reports.
© 2024 PatSnap. All rights reserved.Legal|Privacy policy|Modern Slavery Act Transparency Statement|Sitemap|About US| Contact US: help@patsnap.com